Titanium is a marvel of modern metallurgy, prized across industries like aerospace, medical, chemical processing, and motorsports for its exceptional strength-to-weight ratio, corrosion resistance, and biocompatibility. However, welding titanium presents unique challenges. At elevated temperatures, titanium readily reacts with atmospheric gases like oxygen and nitrogen, leading to embrittlement and contamination – often visible as unsightly “sugar coating.”
Achieving strong, ductile, and corrosion-resistant titanium welds hinges critically on selecting the correct welding consumables – specifically, the tungsten electrodes for TIG welding and the appropriate titanium filler rods. This guide provides expert insights into making the best choices for your titanium welding projects.
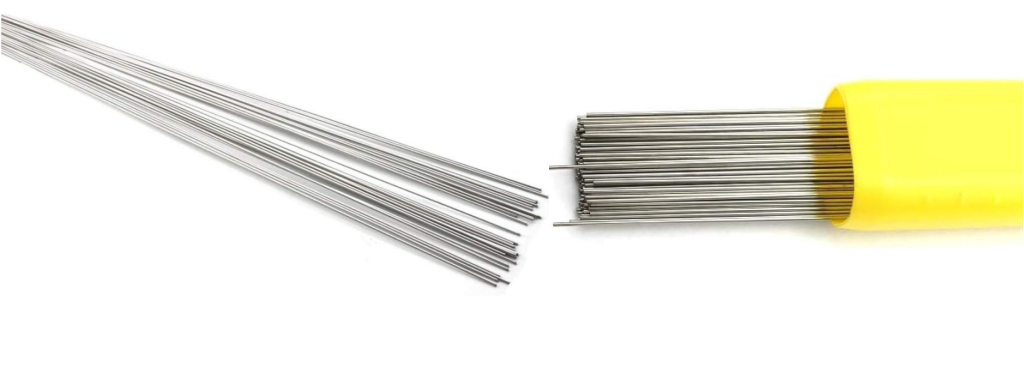
Why Electrode Selection is Paramount for Titanium
Unlike welding steel or aluminum, titanium’s high reactivity demands consumables that introduce minimal contaminants and perform stably under inert gas shielding. The wrong electrode or filler can compromise the weld’s mechanical properties, reduce its corrosion resistance, and lead to costly rework or failure.
Key Electrode Types and Filler Rods for Titanium Welding
For most high-quality titanium welding, Gas Tungsten Arc Welding (GTAW) or TIG welding is the preferred process due to its precision and control, which is essential for minimizing the heat-affected zone and preventing contamination. Here are the primary consumables recommended:
1. Tungsten Electrodes for TIG Welding Titanium
- Recommended Type: 2% Thoriated Tungsten Electrodes (AWS Classification EWTh-2, WT20)
- Why Choose: These have long been the workhorse for DC (Direct Current) TIG welding due to their excellent electron emission, high current carrying capacity, and remarkable arc stability. They maintain a stable arc start and run, which is vital for precise titanium welds.
- Expert Differentiators: The thorium content helps maintain a stable, focused arc and reduces the likelihood of “spitting” tungsten particles into the weld pool, a critical advantage when welding reactive metals like titanium.
- Advantages: Superior arc stability in DC negative polarity (DCEN), long tip life, less prone to contamination transfer.
- Considerations: Thorium is mildly radioactive. While the risk is low with proper handling and ventilation, some users prefer alternatives.
- Alternatives: Ceriated Tungsten (EWCe-2, WC20) or Lanthanated Tungsten (EWLan-1.5/EWLan-2, WL15/WL20) can be viable non-radioactive alternatives, offering good arc stability, though some welders may find WT20 slightly superior for pure DC applications.
Titanium Filler Rods
Recommended Type: ERTi-2 Titanium Welding Rods (AWS A5.16 Specification)
- Why Choose: ERTi-2 is the most common and widely used filler metal for welding commercially pure (CP) Grade 1, 2, 3, and 4 titanium. It matches the properties of CP Grade 2 titanium, offering an excellent balance of strength, ductility, and corrosion resistance.
- Expert Differentiators: ERTi-2 provides strong, sound welds that retain the base metal’s desirable properties, making it suitable for a vast range of applications from chemical processing to general fabrication.
- Advantages: High ductility, good tensile strength, excellent corrosion resistance in many media, readily available, conforms to industry standards.
- Considerations: The specific titanium alloy being welded will dictate the required filler metal grade. For alloys like Ti-6Al-4V, specialized fillers such as ERTi-5 (AWS A5.16) are necessary to match the base metal chemistry and mechanical properties.
- Context: Filler rods are used when joining thicker sections or when building up a weld bead is required. For very thin gauge titanium, autogenous welding (welding without filler) might be possible, but careful control is essential.
Understanding AWS Specifications (A5.16 and A5.11)
- Why Crucial: Adhering to American Welding Society (AWS) specifications like AWS A5.16 (Specification for Titanium and Titanium-Alloy Welding Rods and Bare Electrodes) and AWS A5.11 (Specification for Nickel and Nickel-Alloy Welding Electrodes and Welding Rods… includes some covered electrodes, though less common for high-purity Ti) is fundamental.
- Expert Differentiators: These standards ensure the chemical composition, mechanical properties, and quality control of the welding consumables are consistent and meet rigorous industry requirements, especially critical in aerospace and medical applications.
- Advantages: Guarantees traceability, predictable weld performance, confidence in material integrity.
- Context: Always specify the relevant AWS classification when procuring titanium welding consumables to ensure you are using the correct material for your base metal and application.
Beyond the Electrode: Essential Titanium Welding Practices
Selecting the right consumables is only half the battle. Titanium welding success heavily relies on meticulous technique and preparation:
- Rigorous Cleaning: Base metal and filler material must be impeccably clean, free from oxides, grease, paint, and other contaminants. Use dedicated stainless steel brushes and acetone or approved solvents.
- Superior Shielding: Titanium requires high-purity inert gas (typically Argon, 99.998% or higher) to shield all hot surfaces from the atmosphere. This means:
- Primary Shielding: Gas from the welding torch.
- Secondary Shielding: Using a trailing shield attached to the torch to protect the cooling weld bead and heat-affected zone behind the arc.
- Back Purging: Filling the backside of the weld joint with inert gas to protect the root pass from contamination.
- Tungsten Electrode Preparation: For DC TIG welding titanium, grind the tungsten to a blunted point or a truncated cone with a small flat tip (e.g., 1/32″ flat). Avoid sharp points used for AC welding, as they can detach and contaminate the weld.
- Optimized Parameters: Use appropriate amperage, voltage, and travel speed to minimize heat input and control the weld pool.
- Material Handling: Store titanium base metal and consumables in a clean, dry environment. Handle with clean gloves.
Ensuring Quality and Preventing Defects
A successful titanium weld should appear bright and shiny, possibly with a light straw-colored heat tint. Dark blue, grey, or a white sugary appearance indicates severe atmospheric contamination, rendering the weld brittle and unusable. Proper electrode selection, combined with rigorous cleaning and shielding practices, is your best defense against these critical defects.
Expert Recommendations Summary
For TIG welding commercially pure titanium, the combination of a 2% Thoriated (WT20) or a suitable non-radioactive alternative (like Ceriated or Lanthanated) tungsten electrode with an ERTi-2 filler rod (conforming to AWS A5.16) represents the industry standard for achieving high-quality, contamination-free welds. Always prioritize meticulous cleaning and comprehensive inert gas shielding. For titanium alloys, ensure you select the filler rod specifically designed for that alloy, guided by AWS specifications.
FAQs About Titanium Welding Electrodes
What are the best practices for welding titanium alloys?
Key best practices include: thorough cleaning of base metal and filler; using high-purity inert gas shielding (torch gas, trailing shield, and back purging); selecting the correct AWS-specified filler metal for the specific alloy; preparing the tungsten electrode correctly (blunted tip for DC); minimizing heat input; and welding in a clean, draft-free environment.
How do thoriated tungsten electrodes compare to other types of electrodes for titanium welding?
For DC TIG welding of titanium, 2% Thoriated (WT20) electrodes are often preferred for their exceptional arc stability and electron emission, which helps prevent tungsten inclusions. While other types like Ceriated (WC20) or Lanthanated (WL15/WL20) can also provide stable arcs and are non-radioactive, WT20 is frequently considered the benchmark for demanding DC applications like titanium welding, assuming appropriate safety precautions are followed.
Why is shielding gas so important for titanium welding?
Titanium is highly reactive at welding temperatures and will absorb oxygen, nitrogen, and hydrogen from the atmosphere. This absorption causes the weld and surrounding areas to become brittle and lose corrosion resistance. High-purity inert gas (usually Argon) displaces these harmful atmospheric gases, protecting the molten pool and the hot metal as it cools, ensuring a ductile and sound weld.
Sourcing Quality Titanium Welding Consumables
Achieving excellence in titanium welding requires not only the right techniques but also consistently high-quality materials. When sourcing titanium welding electrodes, filler rods, and bare electrodes, look for suppliers with demonstrated expertise in titanium manufacturing and strict quality control processes. Reputable suppliers will offer products that meet stringent AWS specifications and can potentially provide customized solutions tailored to unique project requirements.