In the demanding world of industrial electrochemistry, reliable and high-performance electrodes are crucial for driving chemical reactions efficiently and sustainably. Titanium-Based Coated Electrodes, also commonly referred to as Ti-based Coated Electrodes, Titanium-Based Metal Oxide Coated Electrodes, or Titanium Metal Oxide Coated Electrodes (depending on the specific coating), represent a cornerstone technology. These electrodes combine the inherent advantages of a titanium substrate with the tailored electrochemical properties provided by a catalytic and conductive surface coating, typically composed of precious metal oxides.
This synergy of materials unlocks enhanced performance, superior corrosion resistance, and extended durability compared to traditional electrode materials, making Ti-based coated electrodes indispensable across a wide array of applications from environmental protection to fundamental chemical production.
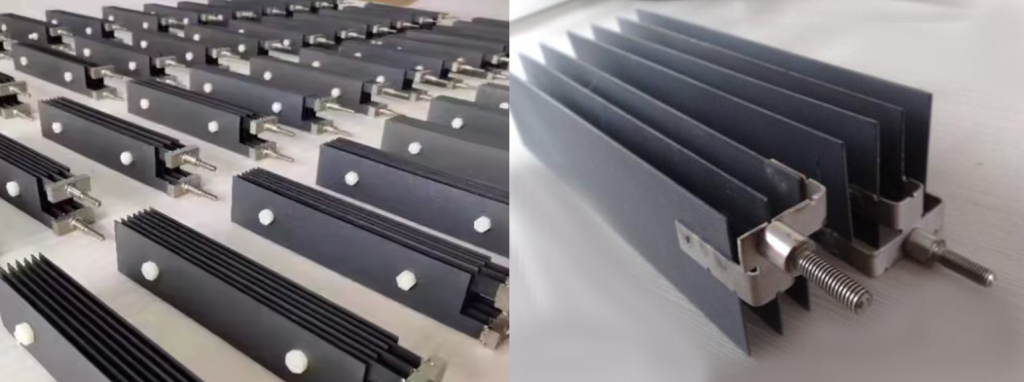
What Are Titanium-Based Coated Electrodes?
At its core, a Titanium-Based Coated Electrode consists of:
- A Titanium Substrate: Made from commercially pure titanium (commonly Grade 1 or Grade 2), which provides exceptional corrosion resistance, mechanical strength, and dimensional stability. Titanium’s ability to quickly form a protective passive oxide layer prevents it from degrading in aggressive electrolytic environments.
- A Conductive & Catalytic Coating: Applied to the titanium surface, this thin layer is the electrochemically active component. Coatings typically include precious metal oxides or mixtures, such as Ruthenium Dioxide (RuO2), Iridium Dioxide (IrO2), Tantalum Pentoxide (Ta2O5), Titanium Dioxide (TiO2), and sometimes Platinum (Pt).
The coating is engineered to lower the overpotential required for specific electrochemical reactions, increase reaction rates, and protect the titanium substrate from excessive anodic oxidation that could render it non-conductive.
Key Features and Advantages
Titanium-Based Coated Electrodes offer a compelling set of advantages:
- High Catalytic Activity: The metal oxide coatings provide numerous active sites, significantly lowering the energy barrier (overpotential) for desired electrochemical reactions, leading to higher reaction rates and efficiency.
- Exceptional Corrosion Resistance: The passive nature of the titanium substrate combined with the chemical stability of the noble metal oxide coating provides robust resistance to attack in harsh acidic, alkaline, and saline electrolytes, as well as complex industrial wastewater.
- Mechanical Strength and Dimensional Stability: The strong titanium base provides structural integrity, while the stable, non-eroding coating ensures the electrode maintains its shape and consistent spacing within the electrolytic cell over long periods (earning them the classification of Dimensionally Stable Anodes or DSAs when the coating confers this property).
- Wide Electrochemical Window: These electrodes can operate stably over a broad range of applied potentials, enabling the catalysis of diverse oxidation and reduction reactions.
- Long Service Life: Engineered coatings are highly durable, allowing electrodes to function effectively for several years, often 2–5 years or more under typical industrial operating conditions, significantly reducing downtime and replacement costs.
- Energy Efficiency: The low operating voltage resulting from high catalytic activity translates directly into substantial energy savings for electrolysis processes.
Common Coating Types and Their Characteristics
The specific composition of the metal oxide coating is crucial as it tunes the electrode’s catalytic selectivity:
- Ruthenium-Based MMO Coated Titanium Electrodes: These coatings, often including RuO2 and TiO2, are primarily optimized for the Chlorine Evolution Reaction (CER). They exhibit high catalytic activity for generating chlorine gas from chloride solutions.
- Applications: Chlor-Alkali industry, wastewater treatment (where hypochlorite generation is desired).
- Applications: Chlor-Alkali industry, wastewater treatment (where hypochlorite generation is desired).
- Iridium-Based MMO Coated Titanium Electrodes: Coatings featuring IrO2, often with stabilizing oxides like Ta2O5 or TiO2. They are favored for the Oxygen Evolution Reaction (OER). Iridium provides excellent conductivity and stability, particularly in acidic environments where oxygen evolution is dominant.
- Applications: Oxygen generation, electrochemical synthesis requiring oxidation, advanced oxidation processes (AOPs).
- Platinum-Based Coated Titanium Electrodes: Electrodes coated with pure Platinum (Pt). Platinum offers excellent electrocatalytic activity for both chlorine and oxygen evolution, as well as hydrogen evolution and other reactions.
- Applications: Electroplating (especially precious metals), fuel cells, specific chemical manufacturing processes. While potentially more costly than MMOs, their unique versatility and activity are valuable in certain applications.
Manufacturing Process
The performance and durability of Ti-based coated electrodes depend significantly on precise manufacturing:
- Coating Application: Metal oxide precursors are applied to the pre-treated titanium substrate using methods like brush coating, thermal decomposition (applying salts and heating), sputtering (vacuum deposition), or electrodeposition.
- Sintering: The coated electrode is heated to high temperatures (typically 400–600°C). This process converts the precursors into a crystalline metal oxide layer, ensuring strong adhesion to the titanium substrate and creating the active, often granular or porous, surface morphology.
- Surface Morphology: The resulting structure (granular, porous, nanotubular, etc.) is critical. A higher effective surface area enhances catalytic activity and enables more efficient electron transfer and mass transport. Nanoscale structures can also improve durability and adhesion.
Applications Across Industries
Ti-based coated electrodes are indispensable in a wide range of sectors:
- Environmental Remediation: Crucial in Wastewater Treatment for electrochemical degradation and decolorization of organic pollutants, removal of ammonia, and advanced oxidation processes (AOPs). Used for treating challenging effluents like landfill leachate and paper mill wastewater.
- Chemical Production: Essential in the Chlor-Alkali Industry for the high-efficiency electrolysis of brine. Used in general Electrochemical Synthesis of various organic and inorganic chemicals.
- Metallurgy: Serve as anodes in Electroplating and Metal Finishing processes (copper, nickel, zinc, precious metals) and in Electrowinning for metal recovery.
- Energy: Used in Hydrogen Production via electrolytic water splitting and as electrodes in certain Fuel Cells and Batteries for energy storage and conversion.
- Other: Including Cathodic Protection systems and Seawater Desalination technologies.
Performance Highlights & Technical Specifications
These electrodes deliver robust performance measured by:
- High effective surface area and electrical conductivity for efficient electron transfer.
- Strong oxidation or reduction capability tailored by the coating.
- Enhanced durability and adhesion through nanoscale coating control.
- Long lifespan (2–5 years typical, often longer with specific coatings and conditions) under industrial operating conditions.
- Capability for customizable coating compositions and thicknesses to optimize performance for specific application requirements.
Summary Table:
Feature | Description |
---|---|
Substrate | Commercially pure titanium (Grade 1 or 2) |
Coating Materials | Metal Oxides (RuO2, IrO2, Ta2O5, TiO2), Pt |
Coating Thickness | 2–15 microns (typical range) |
Typical Current Density | ~50 mA/cm² (variable by application) |
Operating Environment | Acidic, alkaline, saline, industrial wastewater |
Lifespan | 2–5+ years (varies significantly by application/coating) |
Key Applications | Wastewater treatment, Chlor-alkali, Electroplating, Hydrogen production, Synthesis |
Partnering with an Expert Supplier
The quality and tailored performance of Titanium-Based Coated Electrodes depend critically on the manufacturer’s expertise. A leading manufacturer and supplier specializing in titanium and titanium oxide electrodes brings deep knowledge in materials science, advanced coating technologies, and electrochemical engineering. They can provide:
- Expert consultation on selecting the optimal titanium grade, electrode form (plate, mesh, tube, etc.), and coating composition/thickness for your specific application.
- Precise control over the manufacturing process (including thermal decomposition, sputtering, etc.) to ensure coating quality, adhesion, and morphology.
- Rigorous quality control and testing.
- Customized production capabilities to meet unique size, shape, or performance requirements.
Collaborating with such an expert is essential for leveraging the full potential of Ti-based coated electrodes and ensuring reliable, efficient, and long-lasting electrochemical processes.
Titanium-Based Coated Electrodes are vital components in modern electrochemical industries, offering a powerful combination of titanium’s durability and the high catalytic activity and corrosion resistance of precious metal oxide coatings. With distinct coating types tailored for specific reactions like chlorine or oxygen evolution, these electrodes deliver high energy efficiency, stable performance, and extended service life across applications ranging from environmental remediation and chemical production to metallurgy and energy. Their continued development and application are key to advancing sustainable and efficient electrochemical technologies worldwide.
FAQs About Titanium-Based Coated Electrodes
What are the advantages of using MMO coated titanium anodes?
MMO coated titanium anodes offer high catalytic activity, excellent corrosion resistance, dimensional stability (DSA property), long service life (often 2-5+ years), energy efficiency due to low operating voltage, and no contamination of the electrolyte or product.
What are the differences between iridium-based and ruthenium-based MMO coated titanium anodes?
Ruthenium-based coatings are primarily optimized for the Chlorine Evolution Reaction (CER), making them ideal for brine electrolysis (Chlor-Alkali). Iridium-based coatings are typically favored for the Oxygen Evolution Reaction (OER) and offer superior stability and conductivity, especially in acidic environments.
What are the main applications of MMO coated titanium anodes?
Main applications include the Chlor-Alkali industry (chlorine, caustic soda production), Wastewater Treatment (pollutant degradation, disinfection), Cathodic Protection, Electroplating, and Electrochemical Synthesis.
What are the characteristics of titanium-based coated electrodes?
Key characteristics include a corrosion-resistant titanium substrate, a catalytic metal oxide coating (often MMO or Pt), high electrochemical activity, low operating voltage, dimensional stability, long service life, and versatility across various electrochemical environments and reactions.
What is the role of the titanium substrate in these electrodes?
The titanium substrate provides the electrode’s mechanical strength, dimensional stability, electrical conductivity, and crucial corrosion resistance by forming a passive oxide layer, preventing the electrode from dissolving or degrading in harsh electrolytes.