In the dynamic world of electrochemical industries, including the burgeoning field of clean hydrogen production via water electrolysis, the performance and reliability of electrodes are paramount. Stepping beyond the limitations of traditional materials like graphite and lead, Titanium Anodes and Titanium Electrodes have become the standard for high-performance applications. While the terms “anode” and “electrode” are sometimes used interchangeably in general discussion about these materials, technically, “anode” specifically refers to the positive electrode where oxidation occurs during electrolysis. In many applications, the coated titanium component serves as the anode.
A titanium anode or electrode is primarily fabricated from high-purity titanium metal, coated with a thin, electrochemically active layer, most commonly noble metal oxides or platinum. This sophisticated material system leverages titanium’s exceptional corrosion resistance and robust mechanical strength, combined with the superior catalytic properties and electrical conductivity of the coating, resulting in electrodes that are exceptionally durable, efficient, and stable even in the harshest electrochemical environments.
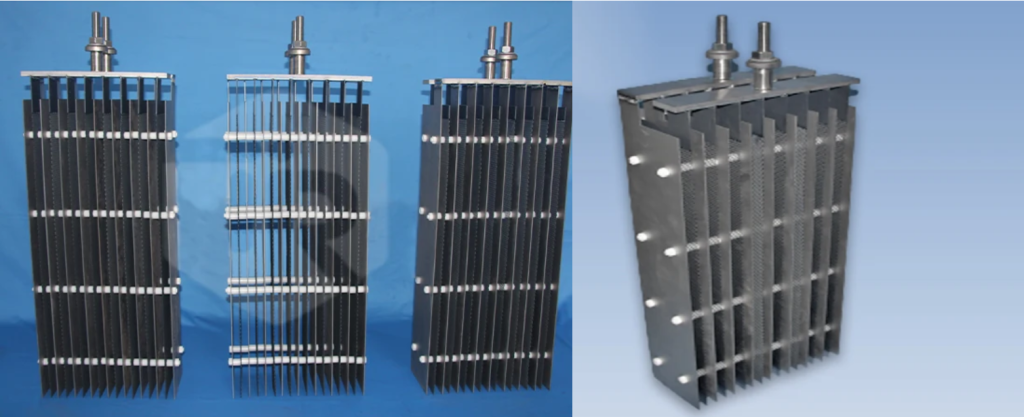
What is a Titanium Anode / Electrode?
At its core, a titanium anode or electrode is a composite structure designed for demanding electrochemical processes:
- Titanium Substrate: Made from commercially pure titanium (typically Grade 1 or 2), this forms the inert base. Titanium is chosen for its outstanding corrosion resistance (due to rapid passivation), high strength-to-weight ratio, and mechanical durability. It acts as a stable, conductive support for the active coating.
- Catalytic Coating: A thin layer (typically 0.5–5 microns, though customizable up to 40 microns or more) of precious metal oxides (like Ruthenium Oxide (RuO2), Iridium Oxide (IrO2), Tantalum Oxide (Ta2O5)) or Platinum (Pt) is applied to the titanium surface. This coating provides the necessary high electrocatalytic activity and conductivity, overcoming the insulating nature of the passive titanium oxide layer that forms naturally on the substrate. These are often referred to as Mixed Metal Oxide (MMO) Coated Titanium Anodes or Platinum Coated Titanium Anodes.
Titanium electrodes are classified as inert electrodes – they do not chemically erode or participate in the reaction itself (unlike sacrificial anodes). Instead, they serve as durable, conductive surfaces that facilitate the efficient transfer of electrons necessary for the desired electrochemical reactions.
Key Features and Advantages
Using titanium anodes and electrodes offers significant benefits over traditional materials:
- Outstanding Corrosion Resistance: The combination of the passive titanium base and the highly stable noble metal oxide or platinum coating provides exceptional resistance to chemical attack in aggressive electrolytes, including strong acids, alkalis, and saline solutions.
- Dimensional Stability (DSA): Coated titanium electrodes are renowned for their Dimensional Stability (DSA). They maintain their shape and size precisely throughout their operational life, preventing deformation, sludge formation, and short circuits. This ensures consistent electrode spacing, stable cell voltage, and reliable process control.
- Low Operating Voltage and Energy Consumption: The catalytic coatings significantly reduce the overpotential required for electrochemical reactions (such as chlorine evolution, oxygen evolution, or pollutant oxidation). This translates directly into a lower operating voltage for the electrolytic cell, resulting in substantial energy savings (10–20% or more) compared to less catalytically active graphite or lead anodes.
- Long Service Life: Engineered coatings are highly durable and resistant to wear. Titanium anodes and electrodes typically offer a long service life, often ranging from 5 to 7 years or more in challenging industrial applications, drastically reducing maintenance frequency and replacement costs compared to traditional electrodes that might last only months.
- Lightweight and Mechanically Strong: Titanium’s high strength-to-weight ratio makes handling and installation easier, particularly for large electrode assemblies.
- Environmentally Friendly: These electrodes are non-toxic and avoid the environmental hazards associated with lead contamination (from lead anodes) or the disposal of spent graphite electrodes. The titanium substrate can often be stripped and recoated.
Common Coating Types for Titanium Anodes / Electrodes
The specific coating applied determines the electrode’s primary catalytic activity and best-suited applications:
- Ruthenium-Iridium (Ru-Ir) Coated Titanium Anodes: Highly catalytic for the Chlorine Evolution Reaction (CER). Primarily used in brine electrolysis (Chlor-Alkali industry) and applications requiring in situ chlorine generation (like swimming pool chlorination).
- Iridium-Tantalum (Ir-Ta) Coated Titanium Anodes: Favored for the Oxygen Evolution Reaction (OER), especially in acidic conditions. Offer high catalytic activity for OER and excellent corrosion resistance, used in electrochemical synthesis and certain metal electrowinning processes.
- Platinum (Pt) Coated Titanium Anodes: Provide versatile, high catalytic activity for a broad range of reactions, including OER, HER (Hydrogen Evolution Reaction), CER, and various oxidation/reduction processes. Commonly used in electroplating, specialized synthesis, and certain water treatment applications.
- Mixed Metal Oxide (MMO) Coated Titanium Anodes: This is a broad category encompassing coatings composed of mixtures of metal oxides (e.g., RuO2,IrO2,Ta2O5,TiO2). The specific mix is tailored for distinct catalytic activities and stability. DSA is the characteristic dimensional stability provided by these coatings.
Applications Across Industries
The versatility and performance of titanium anodes and electrodes make them essential across a wide spectrum of industrial processes:
- Water Electrolysis & Hydrogen Production: Crucial components in electrolyzers used to split water into clean hydrogen and oxygen. Titanium is typically the anode substrate, often coated with Ir-Ta MMO (for OER in acidic PEM electrolyzers) or Ru-Ir MMO (for OER in alkaline electrolyzers). Titanium can also serve as the cathode substrate, often coated with Platinum (for HER in acidic PEM electrolyzers).
- Chlor-Alkali Industry: The foundational electrode material (primarily Ru-Ir coated anodes) for the large-scale production of chlorine, caustic soda, and hydrogen from brine electrolysis.
- Wastewater Treatment: Used in electrochemical oxidation and disinfection systems to remove organic pollutants, pathogens, and other contaminants from various industrial and municipal wastewater streams (various MMO coatings).
- Electroplating and Metal Finishing: Serve as stable, non-contaminating anodes in plating baths for depositing metals like copper, nickel, zinc, chromium, and precious metals (Platinized, Ir-Ta, specific MMOs).
- Cathodic Protection: Employed as durable impressed current anodes to protect steel structures, pipelines, marine vessels (ship hulls, offshore platforms), and storage tanks from corrosion in corrosive environments like soil or seawater (typically MMO coated).
- Chemical Synthesis: Utilized in the electrochemical production of various reagents, fine chemicals, and specialty compounds, offering precise control and efficiency.
- Swimming Pool Chlorination: Used in saltwater chlorinators to electrochemically generate chlorine for disinfection, leveraging their corrosion resistance in saline water.
- Fuel Cells: Titanium components serve as structural elements, current collectors, and sometimes catalyst support layers, facilitating the electrochemical reactions within the fuel cell (e.g., PEM fuel cells).
Manufacturing and Coating Process Basics
Producing high-quality titanium anodes and electrodes involves precise engineering:
- Substrate Pretreatment: Titanium substrates are cleaned and surface-prepared (e.g., sandblasting, acid washing) to create a surface ideal for coating adhesion.
- Coating Application: The active coating materials are applied using methods like brush plating, thermal decomposition (applying metal salt solutions and heating), or sputtering (vacuum deposition).
- Sintering: The coated electrodes are typically sintered at high temperatures (e.g., 400–600°C). This process transforms the applied precursors into a uniform, crystalline, firmly adherent, and catalytically active metal oxide layer.
Industry Examples
- Electroplating Plants: Rely on stable titanium anodes (Platinized or MMO) for uniform plating of metals like copper, nickel, zinc, and precious metals, reducing bath contamination.
- Water Treatment Plants: Utilize titanium anodes (various MMOs) in electrochemical oxidation systems for effective organic pollutant removal and disinfection.
- Chlor-Alkali Plants: Fundamentally depend on high-performance Ru-Ir coated titanium anodes for stable, energy-efficient chlorine and caustic soda production.
- Marine Industry: Protect ship hulls and offshore structures from seawater corrosion using durable MMO coated titanium anodes for impressed current cathodic protection.
- Hydrogen Production Facilities: Employ specially coated titanium anodes (and potentially cathodes) in electrolyzers to generate clean hydrogen fuel efficiently.
Choosing the Right Titanium Anode / Electrode and Supplier
Selecting the optimal titanium anode or electrode requires careful consideration of the specific application, including the desired electrochemical reaction (OER, HER, CER, etc.), the electrolyte composition, temperature, current density, and required lifespan. The choice of coating type, composition, and thickness is critical, as is the physical form of the electrode (plate, mesh, tube, etc.).
Partnering with an expert manufacturer and supplier specializing in titanium anodes and electrodes is crucial. They possess the technical knowledge to recommend the most suitable materials and designs, ensure precise manufacturing and quality control, and offer customized production tailored to your specific requirements, guaranteeing optimal performance and value.
Titanium anodes and electrodes, with their advanced precious metal oxide or platinum coatings on a robust titanium base, are indispensable components in modern electrochemical industries. They provide a superior combination of high catalytic activity, outstanding corrosion resistance, dimensional stability, energy efficiency, and a long service life. Their versatility makes them vital across applications ranging from essential chemical production (like Chlor-Alkali) and environmental solutions (like wastewater treatment) to metal finishing and the increasingly important field of water electrolysis for clean hydrogen generation.
FAQs About Titanium Anodes / Electrodes
What are the differences between titanium anodes and titanium electrodes?
“Electrode” is a general term for any conductor through which electric current enters or leaves an electrolyte. “Anode” specifically refers to the positive electrode where oxidation occurs during electrolysis. In most high-performance applications, the coated titanium component serves as the anode, so the terms are often used interchangeably when discussing these materials, although “anode” is more precise when referring to its polarity in an electrochemical cell.
What are the advantages of using titanium anodes in electroplating?
Advantages in electroplating include their excellent corrosion resistance in plating baths, dimensional stability (DSA property) which ensures consistent plating thickness and quality, long service life reducing downtime, high catalytic activity (for oxygen evolution or other desired reactions), and they do not contaminate the plating bath or the deposited metal.
What are the main applications of titanium anodes in the chemical industry?
Main applications include the Chlor-Alkali industry (producing chlorine, caustic soda), Electrochemical Synthesis of various organic and inorganic chemicals, and the production of oxidizing agents like chlorates and perchlorates.
What are the advantages of using titanium anodes in seawater treatment?
Advantages in seawater treatment include their exceptional corrosion resistance in highly saline and corrosive seawater environments, the ability to efficiently generate disinfectants (like hypochlorite) in situ from the salts in the water via electrolysis, long service life in harsh marine conditions, and dimensional stability in systems like ballast water treatment or biofouling control.
What are the main components of the mixed metal oxide coating on titanium anodes?
The main components of MMO coatings typically include oxides of noble metals such as Ruthenium Oxide (RuO2) and Iridium Oxide (IrO2), often mixed with Tantalum Pentoxide (Ta2O5) and Titanium Dioxide (TiO2). The specific composition is tailored for the intended electrochemical reaction and operating environment.