In the world of high-performance materials and custom craftsmanship, Titanium Damascus, widely known by the proprietary name Timascus, represents a pinnacle of metallurgical art and engineering. Unlike traditional Damascus steel forged from iron alloys, Timascus is a modern composite material created by layering and forge welding different titanium alloys. When processed and colored, it reveals stunning, intricate patterns combined with the vibrant, iridescent hues unique to oxidized titanium.
While often seen in finished items like knife handles and rings, Timascus is commonly supplied in the form of a Titanium Damascus Rod or bar stock. This rod serves as the raw material that craftsmen and manufacturers machine and shape into these exquisite high-end products, blending titanium’s inherent advantages with unparalleled visual appeal.
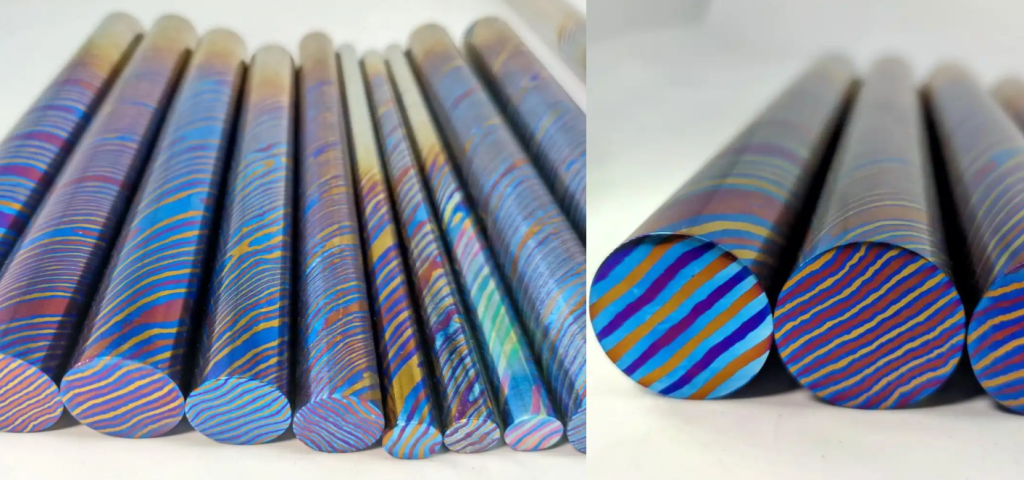
What is a Timascus Rod? (Definition & Core Characteristics)
A Timascus Rod is a solid bar or cylinder made from Titanium Damascus. The material itself is created by:
- Layering: Stacking multiple layers of two or more different titanium alloys, typically commercially pure titanium (CP Ti, like Grade 1 or 2) and Ti-6Al-4V (Grade 5 alloy), though other beta titanium alloys can also be used.
- Forge Welding : Subjecting the layered stack to high temperature (around 850-950°C, near titanium’s beta phase transformation point) and high pressure in an inert atmosphere (like argon). This process achieves diffusion welding, where the layers fuse together at the atomic level without melting.
- Patterning: The resulting billet is then forged, rolled, twisted, carved, or drilled to distort the layers and create complex patterns within the material.
A Timascus Rod is the result of these initial steps, providing a solid piece of layered titanium material ready for subsequent machining, shaping, and finishing.
Core Characteristics of Timascus:
- Lightweight: With a density of only about 4.5 g/cm³, Timascus is roughly 45% lighter than steel, making it ideal for Everyday Carry (EDC) items and accessories.
- High Strength & Corrosion Resistance: Inherits the high strength (Ti-6Al-4V can reach HRC 36-40 hardness) and exceptional corrosion resistance of its parent titanium alloys, resisting attack from seawater, sweat, and many chemicals far better than stainless steel.
- Non-Magnetic: Titanium is a paramagnetic material. Timascus is non-magnetic, suitable for applications near sensitive electronic or magnetic equipment.
- Biocompatibility: Shares the excellent biocompatibility of pure titanium and Ti-6Al-4V, widely used in medical implants, making it safe for prolonged skin contact in jewelry and EDC items.
- Exceptional Color Aesthetics: Through controlled oxidation (heat or anodizing), the surface develops iridescent, multicolored patterns (blues, purples, golds, greens, pinks, etc.) formed by light interference on ultra-thin oxide layers. This provides a unique, customizable aesthetic without dyes or coatings.
The Art and Engineering: How Timascus Rods Get Their Pattern and Color
The beauty of Timascus is a direct result of sophisticated material engineering and controlled processes:
- Layering & Forge Welding: Selecting alloys with subtly different compositions ensures they will respond differently to etching and coloring processes. The precise stacking and diffusion welding create a solid, multi-layered billet from these distinct alloys.
- Pattern Formation: Mechanical manipulation (twisting, carving, etc.) of the forged billet distorts the planar layers into complex, organic patterns that run throughout the material.
- Pattern Revelation (Etching): The patterned surface is treated with mild acids (like a mix of hydrofluoric and nitric acids). Because the different titanium alloys have slightly different resistance to etching, the acid removes material at slightly different rates, creating subtle variations in relief that make the underlying layered pattern visible before coloring.
- Oxidation Coloring (The Magic): This is where the vibrant colors appear. The polished or finished Timascus surface is subjected to controlled oxidation:
- Heat Treatment (Flame Coloring/Burnishing): Heating the titanium in air to precise temperatures between 200°C and 600°C. Different temperatures grow titanium oxide (TiO2) layers of different thicknesses.
- Anodic Oxidation (Anodizing): Submerging the titanium in an electrolyte and applying a specific voltage (typically 20V to 100V). Different voltages grow oxide layers of different thicknesses. The transparent TiO2 layer causes light interference, producing color based on the layer’s thickness. Crucially, the different titanium alloys in adjacent layers form oxide layers of slightly different thicknesses or have subtly different optical properties when subjected to the same heat or voltage. This causes neighboring layers in the pattern to display different colors, creating the material’s signature vibrant, multi-hued appearance.
Manufacturing Challenges
Producing high-quality Timascus Rods is technically demanding:
- High Material Cost: Titanium alloys are significantly more expensive than steel alloys (often 5-10 times the cost). The multi-step forging process can also lead to higher scrap rates.
- Processing Difficulty & Tool Wear: Titanium has low thermal conductivity, which can cause heat buildup and tool wear during machining. Different layers in Timascus have varying hardness, requiring specialized carbide tooling and careful, slower cutting speeds compared to machining homogeneous metals.
- Oxidation Control Sensitivity: Achieving consistent and desired colors requires highly precise control of temperature (for heat coloring) or voltage (for anodizing). This step demands experienced technicians to manage the sensitivity of the oxidation process.
Advantages Over Other Materials (Especially for Rod Stock)
When choosing a material in rod or bar form for high-end custom machining, Timascus offers compelling advantages:
Characteristic | Timascus Rod (Titanium Damascus) | Traditional Damascus Steel Rod | Carbon Fiber Rod |
---|---|---|---|
Weight | Lightweight (4.5g/cm³) | Heavy (7.8g/cm³) | Very Lightweight (1.8g/cm³) |
Corrosion Resistance | Exceptional, no rust, highly chemical resistant | Needs anti-rust maintenance, can corrode | Good (but resin can be UV sensitive) |
Magnetic | Non-Magnetic | Magnetic | Non-Magnetic |
Color & Pattern | Unique Multi-Color Patterns (via oxidation) | Monochrome Layered Patterns (via etching) | Black/Woven Texture |
Machinability | Good (with specific tools/techniques), preserves pattern | Good (pattern revealed after machining/etching) | Requires dust control, brittle |
Price | High (Reflects complex process & materials) | Medium-High | Medium |
Maintenance | Simple cleaning, avoid harsh abrasives/chemicals | Requires oiling to prevent rust, careful etching | Simple cleaning, avoid UV exposure |
Aesthetics | Vibrant, Optical, Unique Layered Hues | Classic Layered Greyscale | Modern, often woven textures |
Using Timascus Rods: Applications & Precision Processing
Timascus rods serve as the premium raw material for creating exquisite, high-value items through precision machining:
- EDC Tools & Tactical Gear: Rods are machined into components for custom knives (handles, bolsters, pocket clips), multi-tools, pry bars, tactical pens, and gun parts where lightweight, durability, corrosion resistance, and unique aesthetics are desired.
- High-End Accessories & Jewelry: Timascus rods and tubes are turned and shaped into watch cases, pen bodies, lighter casings, rings, bracelets, and cufflinks.
- Collectibles & Art Objects: Rods can be sold as collectible items themselves (e.g., signature rods with intricate patterns) or machined into components for larger artistic creations.
Precision Machining: Timascus rods are processed using high-precision techniques like CNC milling, Wire Electrical Discharge Machining (EDM), grinding, and subsequent manual or automated polishing (to a mirror finish) or blasting (for a matte texture). The final vibrant colors are typically applied via heat treatment or anodizing after machining and finishing the surface to reveal the pattern on the final part.
Maintenance and Care
Caring for items made from Timascus rods involves protecting the surface oxidation layer:
- Avoid scratching with hard objects (Titanium’s Mohs hardness is about 6, softer than sapphire or hardened steel).
- Clean regularly with a soft cloth and mild, neutral detergent to remove oils or sweat that could potentially affect the oxide layer over time.
- Avoid prolonged exposure to harsh chemicals or strong UV light, which can potentially alter the color or integrity of the thin oxide film.
- Store in a place away from direct sunlight if concerned about long-term color fading, although the colors are generally quite stable.
Market Positioning
Timascus rods and finished products are positioned at the high-end of the market, appealing to discerning EDC enthusiasts, collectors, custom knife makers, jewelers, and artists. Their value is derived from the complex manufacturing process, the inherent properties of titanium, the artistic patterns, and the unique multicolor aesthetics. Finished items machined from Timascus rods often command premium prices, reflecting the material cost, processing difficulty, and artistic value, commonly ranging from hundreds to thousands of USD. It is often regarded as “portable metal sculpture” or “wearable art”.
Partnering with a Supplier
Sourcing genuine, high-quality Timascus Rods is critical for ensuring predictable patterns, consistent alloy composition, and reliable machinability and coloring. It requires partnering with a reputable supplier specializing in this unique material. Look for suppliers who are transparent about their alloys, manufacturing process, and quality control.
A supplier with expertise in various titanium materials and processing techniques, like Ti Time Company specializing in titanium and titanium oxide products, possesses the foundational knowledge of titanium metallurgy that is crucial to the creation and quality of Timascus. While they may not produce Timascus rods themselves, they understand the properties of the raw titanium alloys (CP and Ti-6Al-4V) that form Timascus and may be able to provide insights or supply high-quality raw materials to Timascus manufacturers, relevant to the high-end market seeking quality titanium materials.
Titanium Damascus Rod (Timascus) is a fascinating material that embodies a fusion of metallurgical science and artistic expression. Supplied as a bar stock, it serves as the premium raw material for machining lightweight, highly durable, non-magnetic, and exceptionally corrosion-resistant components. Its unique layered patterns, brought to life with vibrant, multicolored hues through controlled oxidation, make it a highly sought-after choice for high-end custom knife handles, exquisite jewelry, luxury accessories, and collectible art objects. Timascus rods redefine the possibilities of modern materials in creating functional items of exceptional beauty and lasting value.
FAQs About Titanium Damascus Rod (Timascus)
What are the best uses for a titanium Damascus rod?
Titanium Damascus rods are best used as raw material for machining high-end components where aesthetics and titanium’s properties are valued. Primary uses include custom knife handles and accessories (bolsters, clips), jewelry (rings, watch cases), luxury goods (pens, lighters), tactical gear parts, and collectible art objects.
How does the price of titanium Damascus rods compare to other materials?
Titanium Damascus rods are significantly more expensive than rods made from traditional Damascus steel, stainless steel, or aluminum alloys. The high cost is due to the price of the parent titanium alloys, the complex, multi-step forge welding and patterning process, processing difficulties (tool wear), and the material’s niche market positioning.
Are there any specific brands known for high-quality titanium Damascus rods?
While mentioning specific brands might require market research updates beyond static knowledge, the primary U.S. patent holder who popularized Timascus is often cited. High-quality Timascus is typically sourced from specialized manufacturers or suppliers known for their expertise in titanium metallurgy, diffusion welding, and pattern control. It’s recommended to seek suppliers with a proven track record in this specific material.
What is the difference between AEB-L/302 TWIST and other types of Damascus rods?
AEB-L and 302 are specific stainless steel alloys often layered together to create traditional stainless Damascus steel, and “TWIST” refers to a type of pattern formed by twisting the layers during forging. Titanium Damascus (Timascus) is a fundamentally different material made from titanium alloys (like CP Ti and Ti-6Al-4V). While both show layered patterns, Timascus is lightweight, non-magnetic, highly corrosion-resistant, and gets vibrant colors via oxidation, whereas steel Damascus is heavier, magnetic, prone to rust, and shows patterns via etching in shades of gray/black.
Can titanium Damascus rods be used for jewelry making?
Yes, titanium Damascus rods are highly popular for jewelry making. They are machined into rings, pendants, bracelets, watch components, etc., offering unique layered patterns, vibrant multicolor aesthetics through anodizing, lightweight comfort, biocompatibility, and excellent corrosion resistance for wearable items.