In demanding electrochemical processes across industries like chemical manufacturing, environmental treatment, and metallurgy, the performance and durability of the electrode are paramount. Traditional electrode materials like graphite and lead suffer from wear, corrosion, and dimensional instability. The advent of Coated Titanium Electrodes revolutionized these fields, offering a robust, efficient, and long-lasting alternative. These electrodes, also referred to broadly as Titanium Electrodes with Coating or Coated Ti Electrodes, utilize a titanium substrate coated with various electrocatalytically active and corrosion-resistant materials, most commonly precious metal oxides.
This innovative design combines the exceptional properties of titanium – its lightweight nature, high strength, and outstanding corrosion resistance due to rapid passivation – with the specific catalytic capabilities and enhanced durability provided by the surface coating. The result is a class of electrodes that are Dimensionally Stable Anodes (DSAs), offering significant improvements in energy efficiency, process control, and operational lifespan.
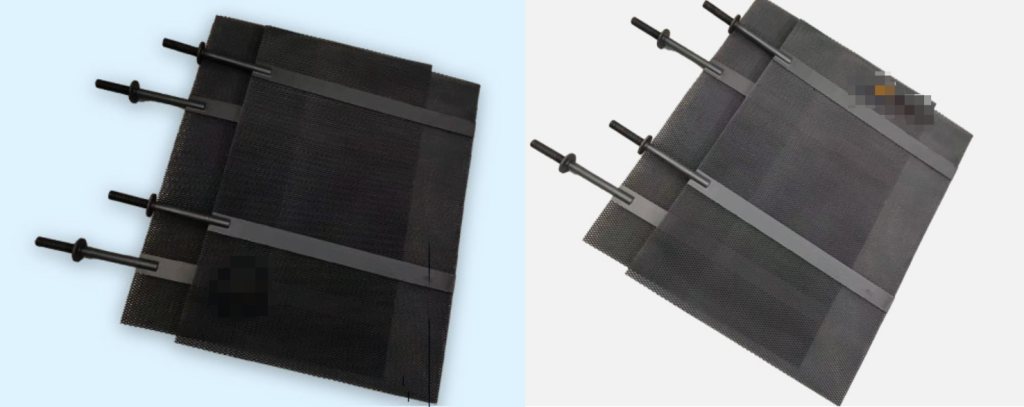
Understanding the Core: Titanium Substrate and Coating
The foundation of any coated titanium electrode is a substrate made from commercially pure titanium, typically Grade 1 or Grade 2. Titanium’s ability to form a protective passive oxide layer in aggressive environments makes it an ideal base material that resists corrosion and maintains structural integrity throughout the electrode’s life.
The key differentiator and performance driver is the coating. Applied through advanced techniques like thermal decomposition or electrodeposition, this thin layer (often microns thick) determines the electrode’s specific electrochemical activity and enhances its resistance to the harsh operating conditions. Common coatings include Platinum (Pt) and various Mixed Metal Oxides (MMO).
Key Types of Coated Titanium Electrodes
While the general term “Coated Titanium Electrode” is used, specific classifications highlight the coating composition and resulting performance characteristics:
Dimensionally Stable Anode (DSA):
- Definition: DSA is less about the coating material itself and more about the functional characteristic. It refers to any coated electrode (usually titanium) that maintains its physical size and shape during electrolysis. This is a significant advantage over traditional consumable anodes that erode or deform.
- Typical Coating: Often MMO coatings, such as blends of Ruthenium Dioxide (RuO2), Iridium Dioxide (IrO2), and Titanium Dioxide (TiO2).
- Benefits:
- Stable Interelectrode Distance: Ensures consistent cell voltage and allows precise control of electrochemical reactions.
- Prevents Short Circuits: Avoids operational failures caused by deformation.
- Reduced Power Consumption: Contributing to energy savings (often cited as 10-20% improvement).
- Long Service Life: Inherits the durability of the coated titanium structure.
- No Contamination: Unlike eroding anodes, DSAs do not introduce material into the electrolyte or product.
- Applications: Widely adopted in chlor-alkali production, wastewater treatment, electrochemical synthesis, and metal finishing.
MMO (Mixed Metal Oxide) Coated Titanium Electrode:
- Composition: Features a coating made from a mixture of metal oxides, most commonly involving precious metals like ruthenium and iridium, often combined with stabilizing oxides like tantalum and titanium oxide.
- Features:
- Exceptional Corrosion Resistance: Highly stable in a wide range of aggressive electrolytes.
- High Electrocatalytic Activity: Provides low overpotential for specific reactions.
- Uniform Current Distribution: Leads to consistent and efficient electrochemical reactions across the electrode surface.
- Extended Lifespan: MMO coatings are engineered for longevity, often exceeding 15 years in continuous operation under proper conditions.
- Reduced Maintenance: Due to long life and stability.
- Applications: The cornerstone of modern chlor-alkali production, vital for water and wastewater treatment (disinfection, pollutant degradation), essential in cathodic protection systems, and used in electrochemical sensors and advanced oxidation processes.
Ru-Ir Coated Titanium Electrode (Ruthenium-Iridium Coated):
- Primary Coating: A specific type of MMO coating where the active layer is primarily composed of Ruthenium Dioxide (RuO2) and Iridium Dioxide (IrO2) on a titanium substrate.
- Key Advantage: Particularly known for its high electrocatalytic activity for the Chlorine Evolution Reaction (CER). Ruthenium provides high activity, while iridium enhances stability and lifespan, especially in brine environments.
- Applications: Predominantly used in the Chlor-Alkali Industry for the electrolysis of brine (NaCl solution) to produce chlorine gas, caustic soda, and hydrogen. Also applied in industrial effluent treatment and salt pool chlorinators for chlorine generation. Typical lifespan ranges from 5 to 8 years in chlor-alkali cells.
Ir-Ta Coated Titanium Electrode (Iridium-Tantalum Coated):
- Primary Coating: Another specific type of MMO coating featuring Iridium Dioxide (IrO2) combined with Tantalum Pentoxide (Ta2O5) on a titanium substrate.
- Key Advantage: Distinguished by its superior corrosion resistance, especially in highly acidic electrolytes, and high catalytic activity for the Oxygen Evolution Reaction (OER). Iridium provides the primary catalytic activity for OER, and tantalum significantly enhances the coating’s stability and durability in challenging conditions.
- Applications: Used extensively in processes involving oxygen evolution in acidic media, such as electrochemical synthesis, electrowinning (e.g., zinc, copper, silver), electroplating (e.g., hard chrome plating baths containing sulfuric acid), water and wastewater treatment (advanced oxidation), and as anodes in some battery and capacitor technologies.
Platinized Titanium Electrode:
- Coating: A relatively thin layer (typically 0.1 to 20 microns) of pure Platinum is coated onto the titanium substrate.
- Properties: Offers electrochemical properties similar to solid platinum metal, providing high conductivity and catalytic activity for various reactions, including oxygen and hydrogen evolution, and certain organic oxidations.
- Applications: Commonly used in metal finishing, specific electroplating baths (where platinum’s unique properties are needed), electrowinning processes, and chemical synthesis.
Key Advantages of Coated Titanium Electrodes (Overall)
The collective benefits of using coated titanium electrodes across various types include:
- Outstanding Corrosion Resistance: The titanium substrate and the precious metal oxide coatings withstand highly aggressive chemical environments.
- Long Service Life: Dramatically extends the operational life compared to traditional electrodes, reducing replacement frequency and downtime.
- High Energy Efficiency: Lower operating voltages due to high catalytic activity lead to significant reductions in power consumption (10-20% or more).
- Stable Electrochemical Performance: DSA properties ensure consistent cell voltage, uniform current distribution, and predictable process outcomes.
- Environmental Benefits: Energy savings contribute to a lower carbon footprint, and their longevity reduces material waste.
- Versatility: Can be designed in various shapes (plates, mesh, tubes, rods, wires) and customized with specific coatings for a wide array of applications.
Applications Overview
Coated titanium electrodes are fundamental components in diverse industrial sectors:
- Chlor-Alkali Industry: Production of chlorine, caustic soda, and hydrogen (primarily Ru-Ir MMO).
- Water & Wastewater Treatment: Disinfection, pollutant removal, electro-oxidation (MMO, Ru-Ir, Ir-Ta).
- Cathodic Protection: Preventing corrosion of metal structures (primarily MMO).
- Electroplating & Metal Finishing: Deposition of metals like copper, zinc, nickel, chrome, rhodium (Platinized, Ir-Ta MMO, other MMOs).
- Electrometallurgy & Electrowinning: Recovery and refining of metals (Ir-Ta MMO, Platinized, other MMOs).
- Electrochemical Synthesis: Production of various organic and inorganic chemicals (MMO, Ru-Ir, Ir-Ta, Platinized).
- Other: Salt pool chlorinators, fuel cells, sensors, and more.
Choosing the Right Coated Titanium Electrode
Selecting the appropriate coated titanium electrode is crucial for optimizing your electrochemical process. Key considerations include:
- The Specific Electrochemical Reaction: Is it primarily chlorine evolution (CER), oxygen evolution (OER), or another redox reaction? This dictates the most suitable coating chemistry (e.g., Ru-rich for CER, Ir-rich for OER in acid).
- Electrolyte Composition and Conditions: The presence of specific ions (chlorides, sulfates), pH levels, temperature, and current density significantly impact coating choice and required durability.
- Required Service Life: Different coatings offer varying lifespans in different environments.
- Electrode Shape and Size: Must fit the cell design (plates, mesh, tubes, rods, etc.).
- Budget and Performance Trade-offs: Balancing initial cost with energy savings and replacement costs over the electrode’s life.
Consulting with an experienced supplier is invaluable in navigating these factors to ensure you select the optimal coated titanium electrode for your needs.
Partnering with an Expert Supplier
The performance, reliability, and longevity of a coated titanium electrode depend significantly on the quality of the titanium substrate and the expertise applied in the coating process. A leading manufacturer and supplier specializing in titanium and titanium oxide electrodes brings the necessary technical knowledge, advanced manufacturing capabilities, and stringent quality control to produce high-performance Coated Titanium Electrodes. Look for a partner who can offer customized production – tailoring the substrate form and dimensions, as well as the coating composition, thickness, and structure – to meet the precise demands of your specific electrochemical application. This ensures optimal efficiency, maximum lifespan, and the best return on your investment.
Coated titanium electrodes, encompassing types like DSAs, MMOs, Ru-Ir, and Ir-Ta coated variants, are transformative technologies in modern electrochemical industries. Their ability to provide high catalytic activity, exceptional corrosion resistance, dimensional stability, and extended service life on a durable titanium substrate makes them indispensable for efficient, reliable, and sustainable production processes, wastewater treatment, and corrosion prevention worldwide. As industrial demands evolve, the versatility and performance of coated titanium electrodes will continue to drive innovation in electrochemistry.
FAQs About Coated Titanium Electrodes
What is the typical lifespan of coated titanium electrodes?
The lifespan varies greatly depending on the coating type and operating conditions. Platinized electrodes typically last several years. MMO-coated electrodes, especially those optimized for specific processes, can last significantly longer, often exceeding 10-15 years, with some specialized MMO coatings rated for up to 20 years in certain applications.
How do coated titanium electrodes perform in different electrolytes?
They perform excellently in a wide range of electrolytes, including strong acids, alkalis, and chloride-rich solutions. The specific coating (e.g., Ru-Ir for brine, Ir-Ta for acidic OER) is chosen and formulated to provide optimal performance and corrosion resistance in the intended electrolyte composition and operating conditions.
What are the main materials used in coated titanium electrodes?
The primary materials are a titanium substrate (usually commercially pure Grade 1 or 2) and the active coating. The coating can be platinum (Pt) or a Mixed Metal Oxide (MMO) layer composed of oxides of precious metals like Ruthenium (Ru) and Iridium (Ir), often combined with stabilizing oxides like Tantalum (Ta) and Titanium (Ti).
What are the applications of coated titanium electrodes in seawater?
Coated titanium electrodes are widely used in seawater, primarily for cathodic protection of marine structures, ships, and pipelines using impressed current systems (typically MMO-coated anodes). They are also used in seawater electrolysis for producing hypochlorite for disinfection or other chemical processes.
What is a Dimensionally Stable Anode (DSA)?
A DSA is a type of coated electrode (usually titanium) that maintains its physical size and shape throughout its operational life, unlike traditional consumable anodes like graphite or lead. This stability is crucial for consistent electrode spacing, stable cell voltage, and reliable process control.