In the demanding landscape of modern electrochemistry, the electrode is far more than just a conductor; it’s a critical catalyst and a key determinant of process efficiency, longevity, and purity. Standing at the forefront of this technology are Coated Titanium Electrodes. These electrodes, often referred to as Coated Ti Electrodes or Titanium Electrodes with Coating, utilize a titanium substrate engineered with a surface layer of precious metals or Mixed Metal Oxides (MMOs) such as platinum (Pt), ruthenium oxide (RuO2), iridium oxide (IrO2), and tantalum oxide (Ta2O5). They marry the exceptional corrosion resistance of titanium with the high catalytic activity of the coating, making them indispensable across electrolysis, metal plating, water treatment, hydrogen production, and more.
The design, manufacturing, and application of these sophisticated components fall under the specialized discipline of Titanium Electrode Engineering. This field focuses on the science and practice required to develop electrodes that deliver optimal performance, efficiency, and durability in specific, often harsh, electrochemical environments.
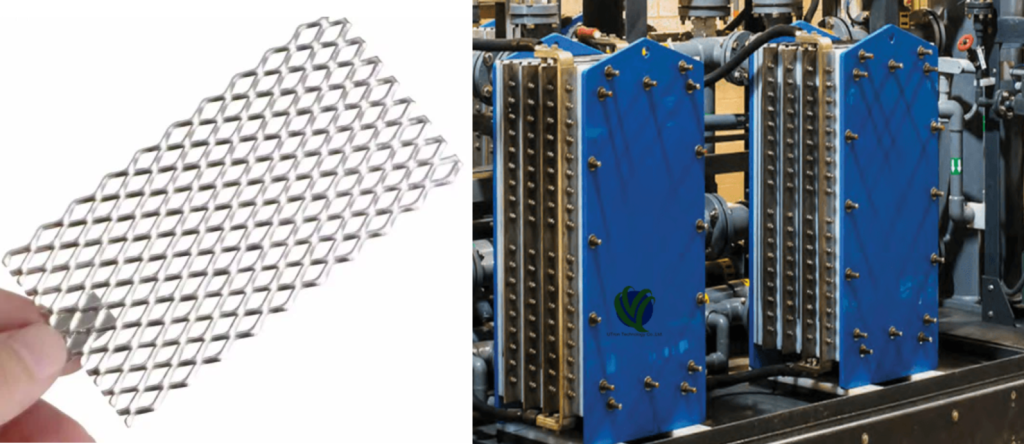
Titanium Electrode Engineering: Materials, Structure, and Design
Effective Titanium Electrode Engineering begins with the fundamental components and their interplay:
Base Material (The Substrate):
- Typically uses high-purity industrial grade Titanium, such as Grade 1 (Gr1).
- Chosen for its lightweight nature, high mechanical strength, and unparalleled corrosion resistance. Titanium’s ability to rapidly form a passive, non-conductive oxide layer protects the underlying metal from degradation in aggressive electrolytes.
Coating Materials (The Catalysts):
- Commonly precious metals or their oxides: Platinum (Pt), Ruthenium Dioxide (RuO2), Iridium Dioxide (IrO2), Tantalum Pentoxide (Ta2O5), and sometimes Titanium Dioxide (TiO2) as a stabilizer or intermediate layer.
- The specific blend and ratio of these materials determine the electrode’s catalytic activity for particular reactions (e.g., Oxygen Evolution, Hydrogen Evolution, Chlorine Evolution).
- Coating thickness is precisely controlled, generally ranging from 0.5 to 20 micrometers, ensuring both effectiveness and economical use of precious metals.
Structure Design:
- Beyond standard plates, meshes, or tubes, Titanium Electrode Engineering explores novel structures.
- Advanced designs, including Double-layer structures and those fabricated via advanced manufacturing techniques like 3D Printing, allow for integrating different functional layers or creating complex geometries.
- These engineered structures can enhance performance at high current densities, improve mass transfer, and optimize the use of precious metals, pushing the boundaries of electrode efficiency and lifespan.
Manufacturing Processes: Engineering the Coating
The performance of a coated titanium electrode is profoundly influenced by how the active layer is applied and treated. Titanium Electrode Engineering involves selecting and mastering various preparation processes:
Thermal Decomposition Method:
- Involves applying solutions of metal salts (precursors) dissolved in organic solvents onto the titanium substrate.
- Repeated heating (sintering) at high temperatures decomposes the salts, forming the metal oxide coating.
- Pros: Relatively simple and cost-effective.
- Cons: Can result in a coating with “mud cracks,” potentially exposing the substrate to corrosion or leading to delamination.
Electrodeposition Method:
- Utilizes an electrochemical process to deposit metal ions from an electrolyte onto the titanium surface.
- Pros: Can achieve uniform coating thickness.
- Cons: Adhesion to the titanium substrate can sometimes be weaker compared to thermal methods.
Sol-Gel Method:
- A nanotechnology-based approach to prepare uniform thin films from a colloidal suspension (sol) that gels and is then heated.
- Pros: Produces dense, homogeneous coatings with good catalytic activity and allows control over film structure at the nanoscale.
Magnetron Sputtering Method:
- A high-end, vacuum-based process where ions are accelerated to bombard a target material (the coating material), causing atoms to be ejected and deposit onto the substrate.
- Pros: Creates highly dense coatings with exceptional adhesion to the titanium substrate, significantly enhancing durability and electrode lifespan, particularly for thin films or specific alloy coatings.
- Cons: Higher cost and complexity compared to wet chemical methods.
The choice of manufacturing process is a critical engineering decision, balancing desired coating properties (density, adhesion, morphology, crystallinity) with economic viability and scalability.
Electrochemical Performance: Engineered for Efficiency and Durability
The result of skilled Titanium Electrode Engineering is an anode exhibiting superior electrochemical characteristics:
- High Catalytic Activity: The precious metal or MMO coating provides abundant active sites, significantly lowering the activation energy required for electrochemical reactions like oxygen evolution (OER), hydrogen evolution (HER), or chlorine evolution (CER).
- Low Working Voltage: Reduced overpotential due to high catalytic activity directly translates into lower voltage requirements for the electrolytic cell, leading to substantial energy savings.
- Excellent Corrosion Resistance: The dual protection of the passive titanium substrate and the stable coating ensures the electrode’s integrity in aggressive acidic, alkaline, or chloride-containing electrolytes.
- Long Service Life: The stable coating prevents the titanium substrate from forming a highly resistive passive oxide layer that would deactivate the electrode. Engineered coatings can achieve operational lifespans of several years, often exceeding a decade in optimized conditions.
- High Current Density Capability: Well-engineered electrodes can sustain high current loads required for intensive industrial processes without excessive degradation or voltage increase.
Key Application Areas Driven by Electrode Engineering
Coated titanium electrodes are critical enablers in numerous industries:
- Hydrogen Production: Essential anodes (and sometimes cathodes) in water electrolyzers (e.g., PEM electrolyzers), offering corrosion resistance in acidic environments and high efficiency for OER and HER.
- Electroplating: Used as non-consumable anodes in plating baths (copper, nickel, zinc, precious metals), ensuring consistent plating quality and bath chemistry.
- Wastewater Treatment: Applied in electrochemical oxidation processes to degrade persistent organic pollutants and disinfect water.
- Chlor-Alkali Industry: Ru-Ir coated titanium anodes are the standard for efficient chlorine and caustic soda production via brine electrolysis.
- Seawater Applications: Used in seawater desalination (electrodeionization) and for generating active chlorine in swimming pools or marine biofouling control due to their resistance to chloride corrosion.
- Cathodic Protection: Serve as durable impressed current anodes to protect pipelines, marine structures, and other buried or submerged metal assets from corrosion.
Partnering with an Expert Supplier: Engineering Your Solution
The complexities of selecting the right substrate, coating material, structure, and manufacturing process highlight that sourcing high-performance coated titanium electrodes requires partnership with a specialist. A leading manufacturer and supplier specializing in titanium and titanium oxide electrodes embodies the expertise in Titanium Electrode Engineering. They possess the deep technical knowledge in material science, electrochemistry, and advanced manufacturing techniques, including the capability for customized production.
An expert supplier can:
- Consult on the optimal coating composition (e.g., Ru-Ir ratio, Ir-Ta ratio) and thickness for your specific electrolyte and reaction.
- Recommend the most suitable manufacturing process for your application’s performance and lifespan requirements.
- Fabricate electrodes in various shapes and sizes (plates, mesh, tubes, rods).
- Develop novel or complex structures, potentially using advanced methods like 3D printing, to meet unique engineering challenges.
- Ensure stringent quality control throughout the production process.
Collaborating with such a partner is essential for obtaining coated titanium electrodes that are precisely engineered for maximum efficiency, durability, and cost-effectiveness in your specific electrochemical application.
FAQs About Coated Titanium Electrodes & Titanium Electrode Engineering
What is a Coated Titanium Electrode?
A Coated Titanium Electrode is an electrode made from a titanium base (substrate) coated with a thin layer of electrocatalytically active and corrosion-resistant material, typically precious metals like platinum or mixed metal oxides (MMOs) like ruthenium and iridium oxides.
What is Titanium Electrode Engineering?
Titanium Electrode Engineering is the specialized discipline focused on the science, design, manufacturing processes, and application optimization of titanium-based electrodes, particularly those with advanced catalytic coatings, to achieve high performance, efficiency, and durability in electrochemical systems.
What are the main materials used in Coated Titanium Electrodes?
The main materials are the titanium substrate (usually commercially pure Grade 1 or 2) and the coating materials, which can include platinum (Pt) or various mixed metal oxides (MMO) containing elements like Ruthenium (Ru), Iridium (Ir), and Tantalum (Ta).
How are Coated Titanium Electrodes manufactured?
Common manufacturing processes include thermal decomposition (applying metal salts and heating), electrodeposition (electrochemically depositing metal), sol-gel methods, and advanced techniques like magnetron sputtering or even 3D printing for complex structures. The choice of method depends on the desired coating properties.
What are the main advantages of using Coated Titanium Electrodes?
Key advantages include high catalytic activity, low operating voltage (energy savings), excellent corrosion resistance, long service life, dimensional stability (DSA property), and the ability to operate at high current densities.
Conclusion
Coated Titanium Electrodes are sophisticated components born from advanced Titanium Electrode Engineering. By skillfully combining the robust chemical and mechanical properties of titanium with the tailored catalytic power of precious metal and MMO coatings, these electrodes overcome the limitations of traditional materials. They deliver unparalleled performance, energy efficiency, and longevity, making them critical drivers in the hydrogen economy, environmental protection, chemical manufacturing, and numerous other vital industries. As the field of Titanium Electrode Engineering continues to evolve with innovations in materials and manufacturing, the capabilities and applications of these high-performance anodes will undoubtedly expand further.