Iridium-Tantalum Coated Titanium Electrodes, often referred to as Ir-Ta Ti Electrodes or Iridium-Tantalum MMO (Mixed Metal Oxide) anodes, represent a pinnacle in electrochemical electrode technology. These high-performance anodes are essential in a wide range of industrial processes, including electrolysis, electroplating, and water treatment, particularly where the Oxygen Evolution Reaction (OER) is dominant or significant. Their effectiveness stems from a sophisticated design that combines a robust titanium substrate with a catalytic mixed oxide coating of iridium (Ir) and tantalum (Ta).
This powerful combination leverages the unique properties of all three elements: titanium’s strength and corrosion resistance, iridium’s exceptional electrocatalytic activity, and tantalum’s remarkable stability and durability, especially in aggressive acidic or chloride-containing environments.
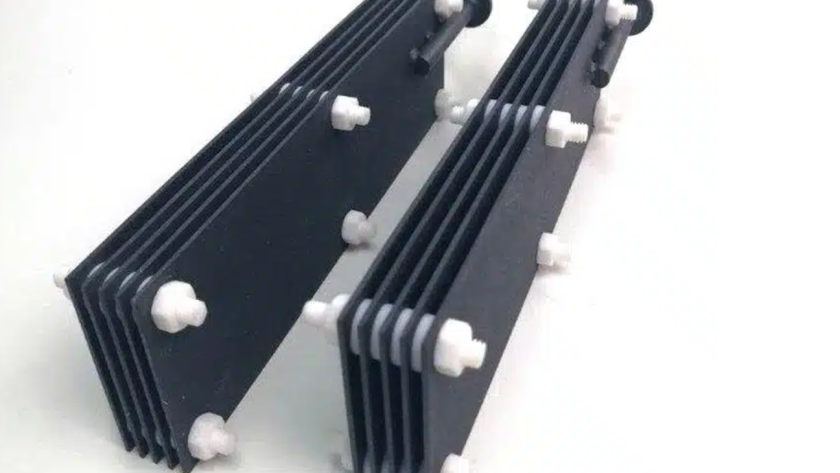
Understanding the Structure and Composition
The efficacy of an Iridium-Tantalum Titanium Electrode is built upon its layered structure:
- Titanium Substrate: The core foundation is pure Titanium, typically Grade 1 or Grade 2. Titanium is selected for its lightweight nature, high strength, and outstanding passive corrosion resistance. It serves as a dimensionally stable, conductive base onto which the active coating is applied.
- Mixed Metal Oxide (MMO) Coating: This is the electrochemically active layer, a precisely controlled mixture of Iridium Dioxide (IrO2) and Tantalum Pentoxide (Ta2O5).
- Iridium (IrO2): A precious metal oxide renowned for its high catalytic activity, particularly for the Oxygen Evolution Reaction (OER) in acidic media. It significantly lowers the anodic overpotential, reducing the energy required for the reaction. Iridium also offers strong resistance to highly oxidative and acidic environments.
- Tantalum (Ta2O5): Known for its exceptional corrosion resistance and stability, especially in harsh chemical conditions including chloride-rich electrolytes. Tantalum acts as a stabilizer within the mixed oxide coating, enhancing its durability, adhesion to the titanium substrate, and overall lifespan.
- Iridium (IrO2): A precious metal oxide renowned for its high catalytic activity, particularly for the Oxygen Evolution Reaction (OER) in acidic media. It significantly lowers the anodic overpotential, reducing the energy required for the reaction. Iridium also offers strong resistance to highly oxidative and acidic environments.
The specific ratio of Ir to Ta is customized based on the intended application to optimize the balance between catalytic activity, selectivity (minimizing side reactions), and lifespan in the particular electrolyte and operating conditions.
Key Performance Advantages
The synergistic properties of the Ir-Ta coating on a titanium base result in several critical advantages:
- Exceptional Corrosion Resistance: Highly stable and resistant to degradation in strong acids, alkalis, and chloride solutions, ensuring long-term performance in harsh industrial baths.
- High Electrocatalytic Activity: Effectively lowers the overpotential for the Oxygen Evolution Reaction (OER), leading to reduced energy consumption and improved electrolytic efficiency.
- Extended Service Life: The stability of the materials and the durability of the coating result in anodes that can operate reliably for several years, minimizing replacement costs and downtime.
- High Current Density Capability: Capable of operating stably under very high current densities, making them suitable for large-scale industrial electrolysis processes demanding high production rates.
- Good Thermal Stability: Maintains catalytic performance and mechanical integrity even at elevated operating temperatures.
- Environmental and Energy Efficiency: Contributes to lower energy consumption, reduced greenhouse gas emissions (compared to energy-intensive alternatives), and less waste due to their long life and potential for recoating.
- Dimensionally Stable: As a type of DSA, they maintain their shape and electrode gap consistently over time, unlike traditional consumable anodes.
Manufacturing Process
The creation of high-performance Iridium-Tantalum Coated Titanium Electrodes involves precise manufacturing steps:
- Substrate Pre-treatment: The titanium base requires thorough cleaning (mechanical and chemical) and etching to ensure optimal surface roughness and cleanliness for strong coating adhesion.
- Coating Application:
- Thermal Decomposition Method: A common method where precursor solutions containing dissolved iridium and tantalum compounds are applied to the pre-treated titanium substrate. The substrate is then heated to high temperatures, causing the compounds to decompose and form the mixed metal oxide coating. This process is repeated multiple times to build up the desired coating thickness (typically 8-15 μm).
- Electrodeposition Method: Involves electrochemically depositing the coating from an electrolyte containing iridium and tantalum ions, controlling parameters like current density and time for uniformity.
- Thermal Decomposition Method: A common method where precursor solutions containing dissolved iridium and tantalum compounds are applied to the pre-treated titanium substrate. The substrate is then heated to high temperatures, causing the compounds to decompose and form the mixed metal oxide coating. This process is repeated multiple times to build up the desired coating thickness (typically 8-15 μm).
- Heat Treatment: After coating application, the electrode undergoes annealing (heat treatment) to enhance the adhesion of the coating to the substrate and optimize its catalytic activity.
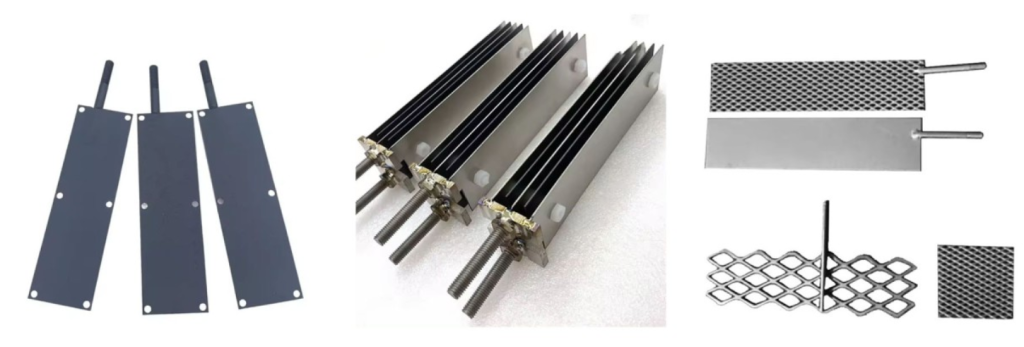
Diverse Applications in Industry
Iridium-Tantalum Coated Titanium Anodes are recognized as optimal electrodes for oxygen evolution in many electrolytic applications, especially where corrosive acidic conditions are present. Their robust performance makes them indispensable in fields such as:
- Electrometallurgy & Electroplating:
- Copper Foil Production: Widely used in the electrolytic production of high-purity copper foil for printed circuit boards. They withstand high current densities (e.g., 7-9 kA/m²) in concentrated sulfuric acid baths (e.g., 120 g/L H₂SO₄), maintaining efficiency and quality. A thin platinum interlayer is sometimes used to enhance life by preventing titanium substrate oxidation, extending anode life to over 2.5 years.
- Zinc Electrowinning: Effective replacement for lead alloy anodes, offering significantly lower oxygen evolution overpotential (reducing energy use) and eliminating lead contamination in the produced zinc. They exhibit long life (5-10 years) even at high current densities (e.g., 10 kA/m²).
- Steel Plate Galvanizing: Used in continuous plating lines for steel, offering lower energy consumption compared to traditional lead electrodes.
- Circuit Board Thick Copper Plating: Address challenges posed by highly acidic electrolytes (e.g., 2 mol/L H₂SO₄).
- Chrome Plating & Rhodium Plating: Replace traditional lead anodes in chrome plating and handle the highly acidic, corrosive rhodium sulfate baths used in rhodium plating, particularly for jewelry.
- Silver Electrowinning: Used as insoluble anodes in the electrolytic refining of silver from rough silver in nitric acid solutions, allowing for efficient silver recovery and low residual silver content in waste streams.
- Copper Foil Production: Widely used in the electrolytic production of high-purity copper foil for printed circuit boards. They withstand high current densities (e.g., 7-9 kA/m²) in concentrated sulfuric acid baths (e.g., 120 g/L H₂SO₄), maintaining efficiency and quality. A thin platinum interlayer is sometimes used to enhance life by preventing titanium substrate oxidation, extending anode life to over 2.5 years.
- Water and Wastewater Treatment:
- Electrochemical Purification: Employed for removing cations at the cathode or eliminating harmful substances via anodic oxidation in acidic or weakly acidic wastewater.
- Electroflotation: Successfully used as oxygen-releasing electrodes in the electroflotation of wastewater containing dispersed substances like peptides and oil. They produce fine gas bubbles (H2 and O2) (50-100 μm) that effectively float contaminants for removal, achieving high efficiency (up to 99.5% removal) in specific industrial setups.
- Electrosynthesis: Used in the electrochemical synthesis of various organic and inorganic compounds, offering longer life and better performance in specific reactions compared to other coating types (e.g., significantly longer life than RuSnTi coatings in Tetramethylammonium Hydroxide production).
- Other Applications: Include applications like the anodic oxidation of aluminum foil and as impressed current anodes for cathodic protection.
Technical Specifications (Reference)
While specific parameters vary based on coating composition and application, typical reference data includes:
- Oxygen Evolution Overpotential: Below 1.45 V (indicating high catalytic activity).
- Coating Thickness: 8-15 μm.
- Precious Metal Content: 15-40 g/m² (varies based on application requirements).
- Working Temperature Range: Generally < 60 ℃ (can be engineered for higher temps).
- pH Range: Adaptable from 1 to 12 (depending on specific coating formulation).
- Service Life: Hundreds to thousands of hours, highly dependent on electrolyte composition, current density, temperature, and presence of contaminants. (In specific industrial applications, lifespans of 2.5 to 10 years are achievable with optimal conditions and coating).
Addressing the Challenge: Organics in OER
While highly stable, it is important to note that in electrochemical systems involving the Oxygen Evolution Reaction (OER) and the presence of organic molecules, platinum group metal oxide coatings (including Ir-Ta) can experience a phenomenon of “rapid active coating detachment” or deactivation. This typically occurs during OER (not necessarily during chlorine evolution or hydrogen evolution) and is often accompanied by a significant increase in electrode potential. Unlike lead alloy electrodes, this rapid failure under specific organic contamination is characteristic of platinum group metal oxide systems. Understanding the electrolyte composition is crucial for selecting or customizing the optimal Ir-Ta coating to mitigate such risks.
Choosing the Right Iridium-Tantalum Electrode
Selecting the appropriate Ir-Ta Ti electrode requires careful consideration of the specific electrochemical process:
- Electrolyte Composition: The chemical makeup (acids, chlorides, sulfates, presence of organics) dictates the optimal Ir:Ta ratio and any necessary modifications to the coating.
- Current Density: Higher current densities require more robust and potentially thicker coatings.
- Desired Service Life: Influences coating thickness and composition.
- Temperature and Pressure: Affect electrode performance and lifespan.
- Electrode Shape: Available in various forms (plates, tubes, meshes, rods, wires) to fit cell design.
Partnering with an experienced manufacturer who can provide technical consultation and customize the electrode design and coating properties is key to ensuring optimal performance and longevity for your specific application.
Partnering with an Expert Supplier
The performance and durability of Iridium-Tantalum Coated Titanium Electrodes are directly tied to the manufacturer’s expertise in titanium metallurgy and advanced MMO coating technology. A leading supplier specializing in titanium and titanium oxide electrodes brings invaluable experience, rigorous quality control, and the critical capability for customized production of Iridium-Tantalum Titanium Electrodes. Such a partner can develop electrodes with specific coating compositions, thicknesses, and forms precisely tailored to meet the unique demands and ensure the success of your electrochemical process.
Iridium-Tantalum Coated Titanium Electrodes are high-performance Dimensionally Stable Anodes that excel in demanding electrochemical applications, particularly those involving oxygen evolution in corrosive environments. By expertly combining the catalytic power of iridium with the stabilizing properties of tantalum on a durable titanium base, these electrodes deliver exceptional energy efficiency, long service life, and reliability. Their versatility and adaptability, especially when sourced from manufacturers capable of customization, make them an indispensable component in modern industrial electrolysis, electroplating, and environmental treatment technologies.
What are the applications of Iridium-Tantalum Titanium Electrodes in water treatment?
In water treatment, they are used for electrochemical disinfection, oxidation of organic pollutants (like COD, BOD), removal of ammonia and nitrates, heavy metal recovery, and in processes like electroflotation to remove suspended solids and emulsions. They are particularly effective in treating acidic or weakly acidic wastewater streams.
How is the corrosion resistance of Iridium-Tantalum Titanium Electrodes?
Their corrosion resistance is excellent. The titanium base is highly stable in many environments, and the Ir-Ta mixed oxide coating is specifically designed to withstand highly corrosive conditions, including strong acids, alkalis, and high chloride concentrations, making them much more durable than traditional electrode materials.
How are Iridium-Tantalum Titanium Electrodes used in the electronics industry?
They are crucial in the electronics industry, particularly for the production of copper foil used in printed circuit boards and in various electroplating processes for circuit boards, connectors, and components (e.g., high-speed copper plating, rhodium plating).