In modern electrochemical technology, particularly in fields like hydrogen production, fuel cells, and advanced environmental treatment, the efficiency and performance of electrodes are paramount. Traditional solid electrodes often limit reaction rates due to mass transport limitations or insufficient active surface area. Porous Titanium Electrodes overcome these challenges by introducing a unique porous structure into the robust titanium material.
These electrodes, also known as Titanium Foam, Porous Titanium Sheet, or Sintered Porous Titanium, are manufactured from titanium base material engineered to possess an interconnected porous network. This structure provides a significantly higher surface area, facilitates efficient transport of gases and liquids, and, when combined with catalytic coatings, creates high-performance electrodes essential for driving complex electrochemical reactions.
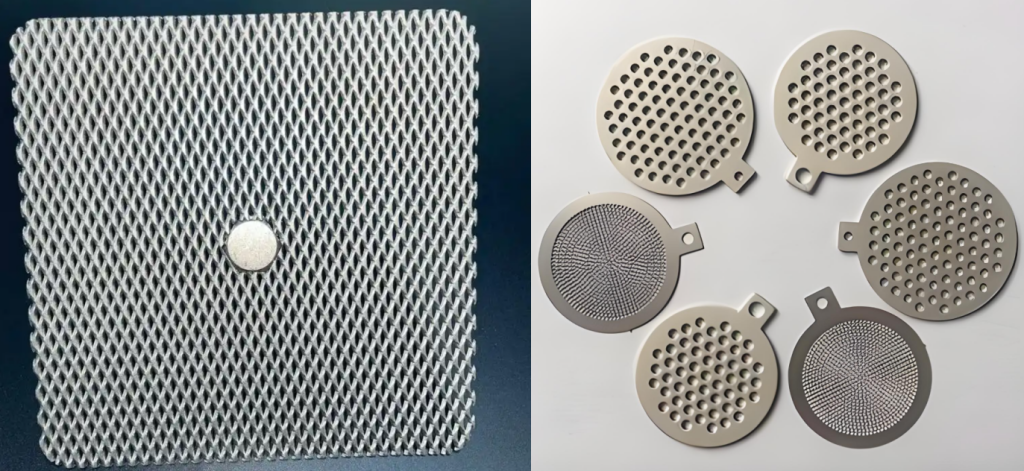
What is a Porous Titanium Electrode? (Definition & Structure)
A Porous Titanium Electrode is a form of titanium material specifically designed to contain a high volume of interconnected pores. It is typically manufactured using techniques like powder metallurgy followed by sintering or advanced methods such as 3D printing and Chemical Vapor Deposition (CVD).
- Base Material: High-purity titanium powder or structures are used, leveraging titanium’s inherent lightweight, high strength, and excellent corrosion resistance.
- Porous Structure: The manufacturing process creates a network of interconnected pores throughout the material.
- Porosity: The percentage of void space within the material, generally ranging from 25% to 50%, can be customized based on application needs.
- Pore Size: The size of the individual pores, typically ranging from 0.2 to 100 micrometers (μm), influences the material’s permeability and capillary action.
- Forms: Common forms include porous titanium foam (often with higher porosity and more open structure) and sintered porous titanium sheet (denser, often thinner).
- Optional Coating: To enhance their electrochemical performance, the porous titanium structures are often coated with noble metals or their oxides, such as Platinum (Pt) or Ruthenium-Iridium (Ru-Ir) oxides. These coatings provide the primary electrocatalytic activity and further improve electrical conductivity and corrosion resistance.
Key Performance Characteristics
The porous structure and optional coating give Porous Titanium Electrodes superior performance characteristics:
- High Specific Surface Area: The intricate porous network dramatically increases the ratio of surface area to volume compared to a solid electrode. This provides significantly more active sites for electrochemical reactions, boosting electrocatalytic efficiency.
- Excellent Gas and Liquid Permeability: The interconnected pores allow for efficient transport of gaseous reactants and products, as well as liquid electrolytes. This is crucial for gas-evolving reactions (like water splitting) as it facilitates the removal of gas bubbles and ensures fresh electrolyte reaches the reaction surface, reducing mass transfer limitations and polarization.
- Excellent Corrosion Resistance: Inherited from the titanium base material, which is highly resistant to acids, alkalis, and high-salinity environments. Catalytic coatings (especially noble metal oxides) further enhance stability in aggressive electrochemical conditions.
- Good Mechanical Strength and Flexibility: Despite their porous nature, these materials retain sufficient mechanical strength and can be fabricated into various shapes and structures suitable for integration into complex electrolytic cells.
- High Electrical Conductivity: While porous, the titanium skeleton provides good electrical conductivity. The addition of conductive noble metal coatings significantly enhances the overall conductivity and efficiency of electron transfer to the active sites.
Fabrication Methods
Creating the desired porous structure and applying coatings requires specialized manufacturing techniques:
- Powder Metallurgy & Sintering: Titanium powder is processed (e.g., pressed or cast as a slurry) and then sintered at high temperatures. This fuses the particles together, creating an interconnected porous network.
- 3D Printing: Advanced additive manufacturing allows for precise control over pore size, shape, distribution, and the overall geometry of the porous structure, enabling highly customized designs.
- Chemical Vapor Deposition (CVD): Can be used to create thin porous films or to apply uniform coatings onto existing porous titanium structures.
- Coating Application: Noble metal coatings (Pt, Ru-Ir MMO, etc.) are typically applied after the porous structure is formed, often using methods like electroplating, sputtering, or thermal decomposition, followed by annealing (heat treatment) to ensure strong adhesion and optimize coating properties.
Applications Across Industries
The unique combination of high surface area, excellent permeability, durability, and catalytic capability makes Porous Titanium Electrodes essential in several key applications:
- PEM Water Electrolysis: Crucial component used as the Porous Transport Layer (PTL) on the anode side (Oxygen Evolution) of PEM electrolyzers. It facilitates the efficient transport of water to the catalyst layer and, most importantly, the rapid removal of evolved oxygen gas bubbles away from the electrode surface, significantly improving efficiency and preventing gas blinding. Sintered porous titanium sheets and ultra-thin porous titanium layers are common forms.
- Fuel Cell Electrodes: Used as catalyst support layers or gas diffusion layers in certain fuel cell designs (e.g., some types of PEMFCs or Solid Oxide Fuel Cells). The high surface area provides abundant sites for catalyst deposition, and the porous structure enables efficient transport of reactant gases and water.
- Wastewater Electrolytic Treatment: High surface area and permeability enhance the efficiency of electrochemical oxidation processes for degrading organic pollutants and disinfecting wastewater by improving mass transport to the electrode surface and providing more active reaction sites.
- Electroplating Auxiliary Electrodes: Used as auxiliary anodes in electroplating baths (especially for precious metals or complex shapes) to help achieve more uniform current distribution and improve plating quality.
- Chemical Industry Electrolysis: Applied in various electrolytic processes where enhanced mass transport and high surface area are beneficial.
- Filtration and Separation: While not an electrochemical application, the base porous titanium material is also widely used for liquid-solid separation and gas filtration due to its controlled pore structure and corrosion resistance.
Forms and Specifications (Typical)
Porous Titanium Electrodes are available in various forms, each with specific characteristics:
- Titanium Foam: Higher porosity (25%-45%), relatively smaller, more uniform pore sizes (0.2-10 μm common for specific grades). High gas permeability.
- Sintered Porous Titanium Sheet: Can be made as thin sheets (0.1-0.25 mm), offering mechanical stability and uniform pore distribution over a larger area (approx 40% porosity).
- Coated Porous Titanium (e.g., Pt Coated): Porous structures coated with Pt, Ru-Ir, or other catalytic materials. Combines porosity benefits with high conductivity and specific catalytic activity.
- Ultra-thin PTL: Highly specialized sintered porous titanium sheets (e.g., ~250 μm thick) specifically engineered for high-performance PEM electrolyzer anode diffusion layers, balancing thickness, porosity, and conductivity.
Typical Performance Indicators:
Feature | Description |
---|---|
Porosity | 25%~50% (Customizable) |
Pore Size Range | 0.2~100 micrometers (μm) |
Thickness | 0.1~0.5 millimeters (mm) or more (Customizable) |
Coating | Platinum (Pt), Ruthenium-Iridium Oxide (Ru-Ir MMO), etc. (Optional) |
Electrical Conductivity | Higher than solid titanium, further enhanced by coating |
Corrosion Resistance | Excellent in strong acid, alkali, high salt |
Mechanical Properties | Good strength and flexibility |
Addressing Key Performance Factors
The effectiveness of Porous Titanium Electrodes is directly linked to their engineered structure and surface properties:
- Impact of Porosity: The percentage and distribution of pores create a large internal surface area, providing numerous reaction sites. The interconnected nature ensures excellent permeability, allowing efficient movement of reactants to the catalyst layer and, critically for gas-evolving reactions like OER or HER, facilitating the rapid escape of product gas bubbles, preventing them from blocking the electrode surface (gas blinding).
- Impact of Coating: While the porous titanium provides structure, corrosion resistance, and conductivity, the applied noble metal coating (Pt, Ru-Ir, etc.) provides the primary catalytic activity needed to lower the overpotential for specific reactions (e.g., OER, HER). The coating also ensures high electrical conductivity across the complex porous network. The porous structure provides a high surface area for the coating, allowing less precious metal to achieve high activity.
Advantages Over Other Electrode Materials (e.g., Carbon-Based)
Compared to porous carbon-based materials sometimes used in electrodes:
- Superior Corrosion Resistance: Titanium is significantly more resistant to corrosion in highly oxidative, acidic, alkaline, or high-salinity environments where carbon materials would quickly degrade, especially on the anode side of many electrochemical cells (like the OER anode in PEM electrolyzers).
- Mechanical Strength and Stability: Porous titanium generally offers better mechanical strength and dimensional stability in wet or corrosive environments compared to some porous carbon forms, which can be brittle or subject to electrochemical/chemical erosion.
Partnering with an Expert Supplier
Manufacturing high-quality Porous Titanium Electrodes with controlled porosity, pore size distribution, and uniform, adherent catalytic coatings is a complex process requiring specialized expertise. It is crucial to partner with a manufacturer and supplier specializing in titanium materials and advanced electrode fabrication.
An expert supplier can provide:
- In-depth knowledge of various porous titanium fabrication methods (powder metallurgy, sintering, 3D printing) and their impact on material properties.
- Expertise in applying specific catalytic coatings (Pt, Ru-Ir MMO, etc.) effectively onto porous structures.
- The capability for customized production – tailoring porosity, pore size, thickness, shape, and coating type/thickness to meet the precise requirements of your specific application (e.g., high-performance PEM, demanding wastewater treatment).
- Rigorous quality control to ensure consistent material properties and electrochemical performance.
Collaborating with such a specialist is essential for leveraging the full potential of Porous Titanium Electrodes in your advanced electrochemical system.
Porous Titanium Electrodes are cutting-edge materials defined by their unique combination of high specific surface area, excellent gas and liquid permeability, and the inherent corrosion resistance of titanium, often enhanced by catalytic noble metal coatings. These properties make them indispensable components, particularly as Porous Transport Layers (PTLs) in PEM water electrolyzers, catalyst supports in fuel cells, and high-efficiency anodes in wastewater treatment. Their continued development and application are key to advancing the fields of clean energy, environmental remediation, and industrial electrochemistry.
FAQs About Porous Titanium Electrodes
What are the main applications of titanium porous electrodes in fuel cells?
In fuel cells, porous titanium electrodes are mainly used as catalyst support layers or gas diffusion layers. Their high surface area allows for efficient loading of catalyst particles, and their porous structure facilitates the transport of reactant gases (hydrogen, oxygen) to the catalyst sites and the removal of product water.
How does the porosity of titanium porous electrodes affect their performance?
Higher porosity generally leads to a larger internal surface area and better permeability. A large surface area provides more active sites for reactions. Good permeability allows for efficient mass transport of reactants and products (like gas bubbles), reducing limitations and improving electrochemical efficiency. The optimal porosity depends on the specific application’s need for surface area versus mechanical strength.
What are the advantages of using titanium porous electrodes over carbon-based electrodes?
The main advantages are superior corrosion resistance in harsh acidic, alkaline, or oxidative environments (especially critical for anode applications like OER in PEM electrolyzers or wastewater treatment) and better mechanical strength and dimensional stability in wet or corrosive conditions compared to many porous carbon materials.
What are the typical specifications for titanium porous electrodes used in PEM electrolyzers?
For use as a Porous Transport Layer (PTL) in PEM electrolyzers, typical specifications might include thicknesses around 0.1-0.5 mm, porosity often around 30-45%, and pore sizes in the range of 5-100 μm (depending on the layer’s specific function), excellent electrical conductivity, and often a noble metal coating (like Pt or Ir-Ta) on the surface facing the catalyst layer.
How does the coating of precious metals on titanium porous electrodes enhance their performance?
The precious metal coating (e.g., Pt, Ru-Ir MMO) provides the primary electrocatalytic activity, significantly lowering the overpotential required for specific reactions (like OER or HER) compared to bare titanium. It also enhances the electrical conductivity across the porous network, ensuring efficient electron transfer from the titanium skeleton to the active catalytic sites.