In the realm of industrial electrochemical processes, the choice of electrode material is paramount to achieving efficiency, durability, and cost-effectiveness. Traditional electrode materials like graphite, lead, and stainless steel often fall short in corrosive environments or demanding applications due to issues like degradation, shape change, or limited catalytic activity. This is where Titanium Electrode Material excels.
More specifically, when referring to the high-performance electrodes widely used today, Titanium Electrode Material primarily signifies a titanium metal substrate coated with catalytically active and corrosion-resistant materials, typically precious metal oxides or platinum. This innovative composite material overcomes the limitations of pure titanium (which passivates and becomes non-conductive under anodic conditions) and combines the best properties of both components.
These materials are the foundation for what are often called:
- Titanium-Based Metal Oxide Coated Electrodes
- Mixed Metal Oxide (MMO) Coated Titanium Electrodes
- Dimensionally Stable Anodes (DSA) (a common name for coated titanium anodes due to their key characteristic)
- Specific types like Ruthenium-Iridium-Titanium Electrodes (Ru-Ir coated)
- Specific types like Iridium-Tantalum-Titanium Electrodes (Ir-Ta coated)
- Platinum Coated Titanium Electrodes
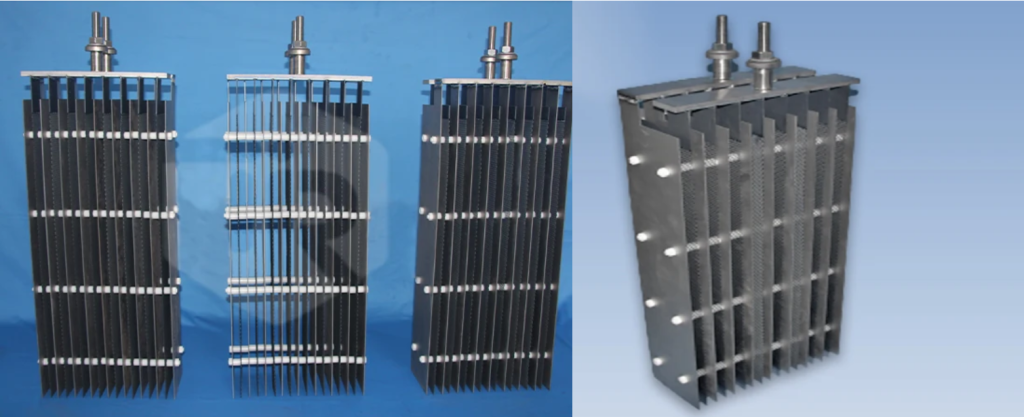
Understanding the Components of Titanium Electrode Material
The effectiveness of Titanium Electrode Material stems from the synergy between its two main components:
Base Material: Titanium
- Typically uses commercially pure Titanium, specifically Grades 1 or 2, known for their formability and excellent corrosion resistance.
- Titanium offers an outstanding strength-to-weight ratio and robust mechanical properties.
- Its key advantage in electrochemical settings is its ability to rapidly form a stable, passive oxide layer when exposed to oxygen or oxidizing environments. While this layer provides exceptional corrosion protection to the underlying metal, it also has low electrical conductivity. This is why a conductive coating is necessary for electrode applications where current needs to flow efficiently.
- Typically uses commercially pure Titanium, specifically Grades 1 or 2, known for their formability and excellent corrosion resistance.
Coating Materials
- Applied as a thin layer (often microns thick) to the pre-treated titanium substrate.
- These are the electrochemically active components that provide conductivity and catalysis.
- Common coating materials include:
- Mixed Metal Oxides (MMO): Mixtures of oxides such as Ruthenium Dioxide (RuO2), Iridium Dioxide (IrO2), Tantalum Pentoxide (Ta2O5), and Titanium Dioxide (TiO2). The specific mix is tuned for desired catalytic activity (e.g., for chlorine or oxygen evolution) and stability.
- Platinum (Pt): A layer of pure platinum provides high catalytic activity for various reactions and excellent conductivity.
- Mixed Metal Oxides (MMO): Mixtures of oxides such as Ruthenium Dioxide (RuO2), Iridium Dioxide (IrO2), Tantalum Pentoxide (Ta2O5), and Titanium Dioxide (TiO2). The specific mix is tuned for desired catalytic activity (e.g., for chlorine or oxygen evolution) and stability.
These coatings provide the high electrocatalytic activity needed to drive electrochemical reactions efficiently, significantly lowering the energy required compared to uncoated titanium or traditional materials.
Key Properties and Advantages
Using Titanium Electrode Material offers numerous benefits compared to conventional electrode materials:
- High Corrosion Resistance: The titanium substrate is inherently resistant to a wide range of harsh chemical environments, including strong acids, alkalis, and saline electrolytes. The stable metal oxide or platinum coating further protects the titanium and maintains activity.
- Stable Electrode Dimensions: Coated titanium electrodes are Dimensionally Stable Anodes (DSA). Unlike consumable electrodes that change shape or erode, they maintain their precise geometry throughout their operational life, ensuring consistent cell voltage and reliable process control. This also eliminates the need for frequent electrode gap adjustments.
- Low Operating Voltage and Energy Consumption: The catalytic coatings significantly reduce the overpotential required for electrochemical reactions. This leads to a lower operating voltage for the electrolytic cell, resulting in energy savings of 10–20% or even more compared to graphite or lead anodes.
- Long Service Life: The combination of a corrosion-resistant base and a durable, non-eroding coating provides a significantly longer operational lifespan. Titanium Electrode Material can often last 5–7 years or more in demanding industrial applications, drastically reducing maintenance and replacement costs compared to traditional electrodes that might only last months.
- Lightweight and Versatile Shapes: Titanium’s high strength-to-weight ratio allows for robust yet lightweight electrode designs. The material can be easily fabricated into various shapes (plates, rods, tubes, meshes, wires) to fit different electrochemical cell configurations and optimize performance for specific applications.
- Prevents Contamination: Since the electrodes are non-consumable and highly corrosion-resistant, they do not introduce contaminants into the electrolyte or final product, which is crucial for processes requiring high purity.
Diverse Types of Titanium Electrode Materials
While the general term “Titanium Electrode Material” applies, the specific coating defines the electrode’s primary function and suitability for different reactions:
- Ruthenium-Iridium-Titanium Electrodes (Ru-Ir coated): Optimized for the Chlorine Evolution Reaction (CER). They exhibit low chlorine overpotential and are ideal for processes like brine electrolysis.
- Iridium-Tantalum-Titanium Electrodes (Ir-Ta coated): Favored for the Oxygen Evolution Reaction (OER), particularly in acidic environments. They offer high efficiency for oxygen generation and excellent corrosion resistance.
- Platinum Coated Titanium Electrodes (Platinized Ti): Provide high catalytic activity for a wide range of reactions, including OER, CER, Hydrogen Evolution (HER), and various oxidation/reduction processes. Widely used in electroplating and specialized electrochemical synthesis.
MMO (Mixed Metal Oxide) is a broad category that includes Ru-Ir and Ir-Ta coatings, among others. The term DSA highlights the key characteristic of dimensional stability common to these coated titanium anodes.
Typical Applications
The outstanding properties of Titanium Electrode Material make it essential across numerous industrial processes:
- Chlor-Alkali Industry: Electrolysis of brine for the production of chlorine, caustic soda (sodium hydroxide), and hydrogen gas.
- Wastewater Treatment: Electrochemical oxidation and disinfection processes to remove organic pollutants, pathogens, and other contaminants from industrial and municipal wastewater.
- Electroplating and Metal Finishing: Used as stable anodes for the deposition of various metals, including copper, nickel, zinc, chromium, and precious metals, ensuring deposit quality and bath stability.
- Cathodic Protection: Applied as impressed current anodes to protect buried pipelines, marine vessels, storage tanks, and other metal structures from corrosion in soil or seawater.
- Chemical Synthesis: Electrochemical production of reagents, fine chemicals, and specialized compounds using various redox reactions.
- Hydrogen Production and Fuel Cells: Used as electrodes in water splitting (electrolysis) devices for clean hydrogen generation and potentially in certain fuel cell designs.
Performance Summary
Aspect | Description |
Base Material | Commercially pure titanium (Grades 1 or 2) |
Coating | Mixed Metal Oxides (RuO₂, IrO₂, Ta₂O₅), Platinum (Pt), or mixtures |
Key Properties | High Corrosion Resistance, Catalytic Activity, Dimensional Stability (DSA), Energy Efficiency |
Typical Shapes | Plates, Rods, Tubes, Meshes, Wires |
Main Applications | Chlor-alkali, Wastewater Treatment, Electroplating, Cathodic Protection, Chemical Synthesis |
Service Life | 5–7 years or more (highly variable by application and coating) |
Energy Saving | 10–20% lower power consumption vs. traditional electrodes |
Choosing the Right Titanium Electrode Material
Selecting the optimal Titanium Electrode Material for a specific application requires careful consideration of the electrochemical reaction, the composition and temperature of the electrolyte, the required current density, the desired lifespan, and the physical constraints of the electrolytic cell. Understanding the different coating types and their catalytic specificities (e.g., Ru-Ir for chlorine, Ir-Ta for oxygen in acid, Pt for versatility) is crucial.
Partnering with an expert supplier specializing in titanium electrode materials is invaluable. They can provide the technical guidance necessary to choose the most suitable material, coating composition and thickness, and physical form to ensure maximum performance, durability, and cost-effectiveness for your specific process.
Partnering with an Expert Supplier
The quality, performance, and reliability of Titanium Electrode Material are directly linked to the manufacturer’s expertise in titanium metallurgy, advanced coating technologies, and electrochemical engineering. A leading manufacturer and supplier specializing in titanium and titanium oxide electrode materials possesses the deep technical knowledge, advanced manufacturing capabilities, and stringent quality control necessary to produce high-performance Titanium Electrode Material. Look for a partner who can offer customized production – tailoring the substrate form, size, and the critical coating material, composition, and thickness – to meet the precise requirements of your application. Such a partner is essential for leveraging the full potential of this advanced electrode material.
Titanium Electrode Material, primarily in the form of coated titanium with precious metal oxide layers, represents a significant advancement in electrochemical technology. Combining the robust corrosion resistance and structural integrity of titanium with the high catalytic activity and durability of coatings like MMOs and Platinum, these materials offer unparalleled performance, energy efficiency, and long service life. Their versatility makes them essential across vital industries, driving cleaner, more efficient, and more sustainable electrochemical processes worldwide.
FAQs About Titanium Electrode Material
Titanium electrodes have what advantages compared to other materials?
Compared to materials like graphite or lead, titanium electrodes offer much higher corrosion resistance, stable electrode dimensions (DSA property), significantly longer service life, lower operating voltage leading to energy savings, lighter weight, and prevent contamination of the electrolyte/product.
Titanium electrodes are used in which industrial processes?
They are widely used in the Chlor-Alkali industry, Wastewater Treatment, Electroplating and Metal Finishing, Cathodic Protection, Chemical Synthesis, and Hydrogen Production/Fuel Cells.
Titanium electrodes have what specific properties?
Key specific properties include high corrosion resistance in harsh electrolytes, high electrocatalytic activity for specific reactions (like CER or OER), dimensional stability (DSA characteristic), good electrical conductivity (due to the coating), and long operational lifespan.
Titanium electrodes are used in electroplating and metal finishing?
Yes, Titanium Electrode Material is widely used as anodes in electroplating and metal finishing to deposit various metals (copper, nickel, zinc, precious metals). They provide stable performance, ensure deposit quality, and resist corrosion in the plating baths.
Titanium electrodes are used in the production of copper foil?
Yes, Titanium Electrode Material, particularly those with coatings suitable for oxygen evolution in sulfate baths (like Ir-Ta MMO), is commonly used as anodes in the electrolytic production of high-purity copper foil for applications like printed circuit boards.