Titanium electrodes are indispensable components in a vast array of industrial electrochemical processes, from producing essential chemicals to treating wastewater and preventing corrosion. Their superiority over traditional electrode materials lies in the combination of titanium’s inherent durability and the enhanced functionality provided by specialized coatings. Understanding the Titanium Electrode Classification is crucial for selecting the right electrode for a specific application, as different types offer distinct performance characteristics. Furthermore, grasping the factors influencing the Titanium Plate Electrode Price is essential for effective budgeting and procurement.
This guide delves into the primary ways titanium electrodes are classified, explores their key applications, and provides insight into the pricing of a common form factor – the titanium plate electrode.
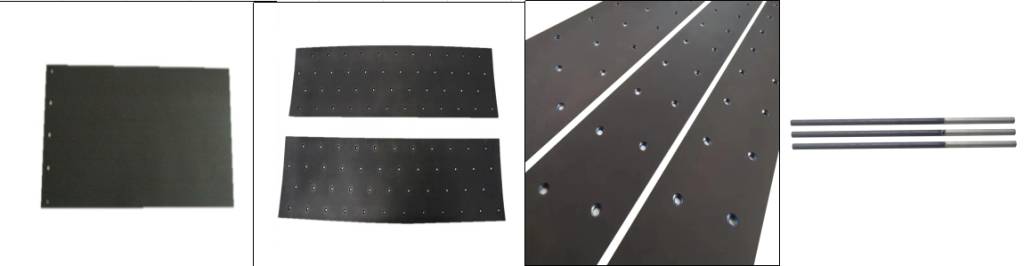
The Basis of Titanium Electrode Classification
Titanium electrodes are categorized based on several key attributes, reflecting their design and intended use in electrochemical cells:
- By Coating Material: This is arguably the most significant classification, as the coating dictates the electrode’s catalytic activity, selectivity for specific reactions (like oxygen evolution, chlorine evolution, or hydrogen evolution), and resistance to the electrolyte.
- By Physical Form/Structure: Electrodes are fabricated in various shapes like plates, mesh, tubes, rods, and wires to suit different reactor designs, current distribution requirements, and fluid flow conditions.
- By Intended Electrochemical Application: While related to coating and form, electrodes are often optimized and classified based on the process they are designed for (e.g., chlor-alkali anodes, water treatment electrodes, cathodic protection anodes).
Major Classifications by Coating Type
The coating applied to the titanium substrate is key to the electrode’s performance. Here are the major types classified by their coating:
Platinized Titanium Electrode:
- Coating: A thin layer of pure Platinum (Pt) is deposited onto the titanium substrate.
- Key Features: Offers high electrical conductivity and excellent catalytic activity for various reactions, similar to solid platinum but at a lower cost due to the titanium base.
- Typical Applications: Water electrolysis, electrochemical synthesis, fuel cells, sensors, and metal finishing/electroplating where platinum’s specific catalytic properties are required.
- Coating: A thin layer of pure Platinum (Pt) is deposited onto the titanium substrate.
Ruthenium-Iridium-Titanium Electrode (Ru-Ir Coated):
- Coating: Typically features a mixed metal oxide coating primarily composed of Ruthenium Dioxide (RuO2) and Iridium Dioxide (IrO2), often with a base layer containing titanium oxide.
- Key Features: Known for excellent corrosion resistance and high catalytic activity, particularly for the Chlorine Evolution Reaction (CER). Stable in acidic and high-temperature brine environments.
- Typical Applications: Widely used in Chlor-Alkali electrolysis for chlorine, caustic soda, and hydrogen production, industrial wastewater treatment (where chlorides are present), and electrochemical sensors.
- Coating: Typically features a mixed metal oxide coating primarily composed of Ruthenium Dioxide (RuO2) and Iridium Dioxide (IrO2), often with a base layer containing titanium oxide.
Iridium-Tantalum-Titanium Electrode (Ir-Ta Coated):
- Coating: Features a mixed metal oxide coating primarily of Iridium Dioxide (IrO2) and Tantalum Pentoxide (Ta2O5).
- Key Features: Offers superior corrosion resistance, especially in aggressive acidic conditions, high electrical conductivity, and strong catalytic activity for the Oxygen Evolution Reaction (OER). Tantalum enhances stability and durability.
- Typical Applications: Used in electrolysis and electrochemical synthesis (particularly OER), electrochemical sensors, certain battery and capacitor types, and corrosion protection systems in acidic environments.
- Coating: Features a mixed metal oxide coating primarily of Iridium Dioxide (IrO2) and Tantalum Pentoxide (Ta2O5).
Mixed Metal Oxide (MMO) Coated Titanium Electrode:
- Coating: This is a broader category referring to coatings composed of a mixture of metal oxides (e.g., RuO2, IrO2, Ta2O5, TiO2). Ru-Ir and Ir-Ta coatings are specific types of MMO coatings.
- Key Features: MMO coatings are synonymous with Dimensionally Stable Anodes (DSA) because they maintain their size and shape during electrolysis, offering stable performance, low operating voltage, energy efficiency, and long service life without contaminating the process.
- Typical Applications: Cornerstone in Chlor-Alkali production, crucial for wastewater treatment, essential for cathodic protection, and used in various electroplating processes.
- Coating: This is a broader category referring to coatings composed of a mixture of metal oxides (e.g., RuO2, IrO2, Ta2O5, TiO2). Ru-Ir and Ir-Ta coatings are specific types of MMO coatings.
Lead Dioxide (PbO₂) Coated Titanium Electrode:
- Coating: A coating of Lead Dioxide (PbO2).
- Key Features: Suitable for specific strong oxidizing environments where other coatings might degrade.
- Typical Applications: Used in the production of strong oxidizers like perchlorates and in certain specialized wastewater treatment processes.
Classification by Physical Form
Titanium electrodes are also classified by their shape, engineered to fit different cell designs and optimize current distribution and mass transfer:
- Titanium Mesh Electrodes: Offer a high surface area relative to their volume, allowing for efficient current distribution and fluid flow-through.
- Titanium Plate Electrodes: Provide a sturdy, flat surface, suitable for stackable cell designs and applications requiring a rigid anode structure.
- Titanium Tube Electrodes: Ideal for applications requiring flow-through reactors or cathodic protection systems where anodes are inserted into structures.
- Titanium Rod or Wire Electrodes: Used in specific laboratory or industrial cell configurations.
Titanium Plate Electrodes: A Common Form Factor
Titanium Plate Electrodes are one of the most widely utilized forms due to their structural rigidity and ease of installation in various cell configurations. They serve as a versatile platform for applying the different types of catalytic coatings mentioned above.
Understanding Titanium Plate Electrode Price
The cost of a titanium plate electrode is not fixed; it’s a variable influenced by several critical factors. Understanding these factors helps in accurately estimating costs and making informed procurement decisions.
Factors Affecting Price:
- Material Grade of Titanium: While commonly Grade 1 or Grade 2 pure titanium is used, the specific grade can influence the price. Higher grades or specific alloys may have different costs.
- Coating Type and Thickness: This is the most significant factor. The use of precious metals (Platinum, Ruthenium, Iridium) drives up the cost. The specific composition of MMO coatings (e.g., the ratio of expensive Iridium to less expensive Ruthenium or Tantalum) and the total thickness of the active coating layer directly impact the price.
- Size and Thickness of the Plate: Larger surface area and thicker titanium plates require more raw material, directly increasing the base cost.
- Supplier and Quantity: Purchasing directly from experienced manufacturers may offer better value than intermediaries. Bulk orders typically qualify for unit price reductions. Supplier reputation and quality control also factor into pricing.
- Customization: Electrodes with non-standard sizes, shapes, hole patterns, or specialized coating compositions tailored for unique applications will cost more than standard products.
Approximate Price Range Examples (Illustrative):
Based on market data, here are approximate price ranges for typical titanium plate electrodes. Please note that these are highly variable examples for specific sizes (e.g., 100x100mm or similar small plates) and actual prices will depend heavily on the exact specifications, coating thickness, quantity, and current market conditions.
- Uncoated Grade 1 or 2 Titanium Plate: ~$13.50 – $18.50 per piece (small size)
- MMO (Standard Ru-Ir-Ti or Ru-Ir-Sn) Coated Titanium Plate Electrode: ~$27.00 – $60.00 per piece (e.g., 100x100mm)
- Ru-Ir Coated Titanium Plate Electrode (Specific Mix): ~$30.00 – $60.00+ per piece (e.g., 100x100mm)
- Iridium-Tantalum (Ir-Ta) Coated Titanium Plate Electrode: Prices can vary widely, often comparable to or higher than Ru-Ir depending on Ir content.
- Platinum-Coated Titanium Plate Electrode: ~$28.00 – $60.00+ per piece (e.g., 100x100mm), heavily dependent on the specified platinum thickness.
These figures highlight that the addition of a catalytic coating, particularly one containing precious metals, is the primary driver of cost difference between raw titanium and a functional electrode.
Key Applications Enabled by Titanium Electrodes
Regardless of the specific classification by coating or form, titanium electrodes are fundamental to processes requiring efficient, durable, and corrosion-resistant anodes:
- Chlor-Alkali Production: (Ru-Ir MMO)
- Water and Wastewater Treatment: (MMO, Ru-Ir, Ir-Ta, PbO₂)
- Cathodic Protection: (MMO)
- Electroplating and Metal Finishing: (Platinized, Ir-Ta, specific MMOs)
- Electrometallurgy and Electrowinning: (Ir-Ta, Platinized, specific MMOs)
- Electrochemical Synthesis: (Various coated types depending on reaction)
- Seawater Electrolysis & Disinfection: (Ru-Ir MMO, specific MMOs)
The advantages of using titanium electrodes in water treatment specifically include their corrosion resistance in various water chemistries, ability to generate powerful oxidants in situ (like hypochlorite from chlorides or hydroxyl radicals via OER), energy efficiency due to low overpotential, and long life, which reduces maintenance in crucial infrastructure.
Choosing the Right Electrode and Supplier
Navigating the various classifications and cost factors requires expertise. Selecting the optimal titanium electrode involves:
- Clearly defining the electrochemical application, including the specific reaction, electrolyte composition, operating temperature, current density, and desired lifespan.
- Understanding which coating type (Platinized, Ru-Ir, Ir-Ta, other MMO, PbO2) is best suited for that specific chemistry and reaction.
- Determining the required physical form (plate, mesh, tube, etc.) and dimensions for the electrolytic cell.
- Considering the budget while focusing on the total cost of ownership (initial price + energy savings + replacement frequency) rather than just the upfront cost.
Partnering with an experienced manufacturer and supplier specializing in titanium electrodes is invaluable. Such a partner can provide technical guidance on classification, recommend the optimal design and coating for your application, ensure high-quality manufacturing, and offer customized production tailored to your exact specifications, providing transparent pricing based on your unique needs.
FAQs About Titanium Electrodes
What are the main applications of titanium electrodes?
Titanium electrodes are widely used in the Chlor-Alkali industry, Water and Wastewater Treatment, Cathodic Protection, Electroplating and Metal Finishing, Electrometallurgy/Electrowinning, Electrochemical Synthesis, and Seawater Electrolysis/Disinfection.
What are the different types of titanium electrodes?
Titanium electrodes are classified mainly by their coating, including Platinized, Ruthenium-Iridium (Ru-Ir) Coated, Iridium-Tantalum (Ir-Ta) Coated, Mixed Metal Oxide (MMO) Coated (a broad category that includes Ru-Ir and Ir-Ta types), and Lead Dioxide (PbO2) Coated electrodes. They are also classified by form (Plate, Mesh, Tube, Rod).
What are the advantages of using titanium electrodes in water treatment?
Advantages include excellent corrosion resistance in various water chemistries, ability to perform electrochemical oxidation of pollutants and generate disinfectants in situ with high efficiency (low overpotential), dimensional stability (DSA property) for reliable operation, and long service life reducing maintenance.
What does MMO stand for in titanium electrodes?
MMO stands for Mixed Metal Oxide. MMO coatings are composed of a mixture of metal oxides, often including precious metal oxides (RuO2, IrO2) and stabilizing oxides (Ta2O5, TiO2). They are known for their high catalytic activity and durability, resulting in Dimensionally Stable Anodes (DSAs).
Why does the coating type significantly affect the price of a titanium electrode?
The coatings often contain expensive precious metals like Platinum, Ruthenium, and Iridium. The specific type of precious metal, its percentage in the coating, and the total coating thickness required for a given application are major cost drivers.
Conclusion
Titanium electrode classification is primarily based on the critical catalytic coating applied to the titanium substrate, which determines performance characteristics like the reaction catalyzed, corrosion resistance, and lifespan. Physical form is another key classification aspect influencing application suitability. While the Titanium Plate Electrode Price is influenced by factors like titanium grade, size, and quantity, the coating type and thickness, particularly the precious metal content, are the most significant determinants of cost. Understanding these classifications and price drivers empowers industries to select the most effective and economical titanium electrodes for their vital electrochemical processes.