As the global focus shifts towards clean energy, the production of hydrogen through water electrolysis is gaining increasing prominence. Water electrolysis, the process of splitting water molecules (H2O) into hydrogen gas (H2) and oxygen gas (O2) using electricity, relies heavily on the performance and durability of the electrodes used. At the heart of efficient and sustainable water splitting technology are Titanium Electrodes for Water Electrolysis.
These specialized electrodes are engineered to provide the high catalytic activity and corrosion resistance necessary to drive the water splitting reaction efficiently over extended periods. They typically consist of a titanium substrate coated with noble metal oxides or platinum, combining the inherent advantages of titanium with advanced catalytic surfaces tailored for the specific reactions involved in water electrolysis.
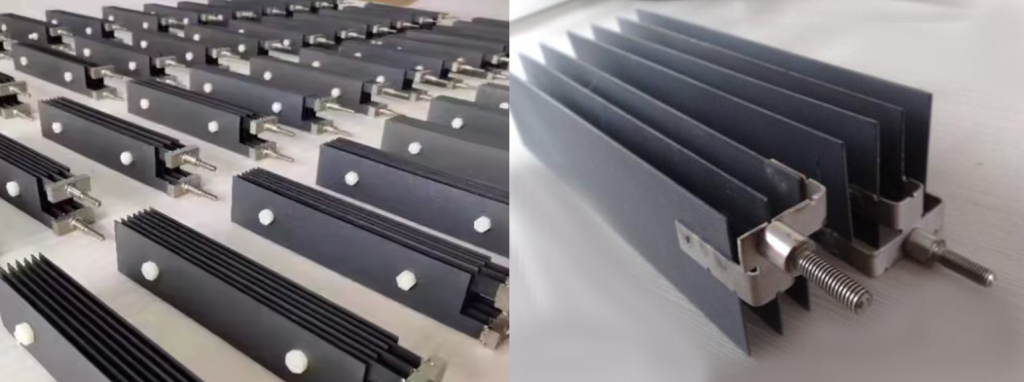
What Makes a Titanium Electrode Suitable for Water Electrolysis?
A Titanium Electrode designed for water electrolysis is a sophisticated component composed of two primary parts:
- The Titanium Substrate: Made from commercially pure titanium (commonly Grade 1 or Grade 2), this provides the structural integrity, lightweight nature, and crucial corrosion resistance required to withstand the often aggressive acidic or alkaline electrolytes used in electrolyzers. Titanium forms a stable passive oxide layer that protects it from degradation, ensuring the electrode’s long-term stability.
- The Catalytic Coating: Applied to the titanium surface, this thin layer is composed of electrochemically active materials, most often noble metal oxides like Ruthenium Oxide (RuO2), Iridium Oxide (IrO2), Tantalum Oxide (Ta2O5), or Platinum (Pt). These coatings are essential because the passive oxide layer on pure titanium is not sufficiently conductive or catalytically active for efficient water splitting. The coating significantly lowers the overpotential (the extra voltage needed beyond the theoretical minimum) required for the anode (Oxygen Evolution Reaction, OER) and cathode (Hydrogen Evolution Reaction, HER) reactions.
Key Features and Advantages
Titanium Electrodes offer compelling advantages for water electrolysis applications:
- High Catalytic Activity and Low Overpotential: The noble metal oxide or platinum coatings significantly reduce the activation energy for the OER and HER, leading to lower operating voltages and energy savings of 10–20% or more compared to traditional electrode materials.
- Excellent Corrosion Resistance: The combination of the passive titanium substrate and the stable noble metal coating ensures remarkable resistance to degradation in the acidic, alkaline, or saline electrolytes used in various electrolyzer types, guaranteeing long-term stable operation.
- Dimensional Stability: Titanium electrodes maintain their precise size and shape throughout their operational life. This Dimensional Stability (DSA property) is critical for maintaining consistent electrode spacing, preventing short circuits, and ensuring stable cell voltage and current density for reliable hydrogen production.
- Long Service Life: Engineered coatings are highly durable. Titanium electrodes for water electrolysis typically boast a service life ranging from 5 to 7 years or more, significantly exceeding the lifespan of consumable graphite or lead electrodes, which reduces maintenance and replacement costs.
- Versatility Across Electrolyzer Types: Suitable for various water electrolysis systems, including traditional alkaline electrolyzers (often using Ru-Ir or Ir-Ta based MMO anodes) and advanced Proton Exchange Membrane (PEM) electrolyzers (typically using Ir-based anodes for OER and Pt-based cathodes for HER due to the acidic environment). They are used in everything from small household hydrogen water machines to large-scale industrial hydrogen production plants.
- Lightweight and Customizable: Titanium’s high strength-to-weight ratio makes the electrodes relatively lightweight. They can be easily fabricated into various forms such as plates, meshes, rods, tubes, and wires, allowing for customized designs to fit different electrolyzer configurations and optimize performance.
Common Coatings for Water Electrolysis
The specific coating applied determines the electrode’s primary catalytic function and suitability for different electrolyte chemistries in water electrolysis:
- Ruthenium-Iridium Oxide (Ru-Ir) Coatings: Common MMO (Mixed Metal Oxide) coatings often used as anodes in alkaline or neutral water electrolysis due to their high catalytic activity for the Oxygen Evolution Reaction (OER).
- Platinum (Pt) Coatings: Widely used as cathodes in acidic PEM electrolyzers due to their high catalytic activity for the Hydrogen Evolution Reaction (HER). Platinum can also catalyze the OER.
- Iridium-Tantalum Oxide (Ir-Ta) Coatings: Common MMO coatings often used as anodes in acidic PEM electrolyzers. Iridium is a highly active catalyst for the OER in acidic conditions, and Tantalum enhances the coating’s stability.
- Custom MMO Coatings: Manufacturers can tailor the blend of oxides (RuO2,IrO2,Ta2O5,TiO2) to optimize performance for specific operating conditions, such as varying electrolyte concentrations or temperatures.
Working Principle: Catalyzing Water Splitting
In water electrolysis, water is split into hydrogen and oxygen gases through redox reactions occurring at the anode and cathode:
- Anode Reaction (Oxidation): Water molecules or hydroxide ions lose electrons to form oxygen gas. In alkaline conditions: 2OH−→21O2+H2O+2e−. In acidic conditions: H2O→21O2+2H++2e−.
- Cathode Reaction (Reduction): Water molecules or protons gain electrons to form hydrogen gas. In alkaline conditions: 2H2O+2e−→H2+2OH−. In acidic conditions: 2H++2e−→H2.
Titanium electrodes, with their specialized coatings, act as highly efficient catalysts for these reactions. The anode coating (often Ru-Ir or Ir-Ta based MMO) significantly reduces the overpotential for the OER, allowing oxygen to evolve efficiently. The cathode coating (often Platinum) reduces the overpotential for the HER, allowing hydrogen to evolve efficiently.
Applications in Water Electrolysis and Related Areas
Titanium electrodes are fundamental to technologies relying on water splitting:
- Hydrogen Production: Essential components in electrolyzers for large-scale industrial hydrogen production (e.g., for ammonia synthesis, refineries), fueling fuel cell vehicles, and in small-scale household hydrogen water generators.
- Water Treatment and Disinfection: Used in electrochemical water treatment systems that generate oxidizing agents (like ozone or hypochlorous acid) in situ by splitting water or oxidizing chloride ions present in the water. Examples include disinfection water machines and systems for treating circulating cooling water or ballast water.
- Chlor-Alkali Industry: While primarily focused on brine electrolysis, the process also involves water splitting and utilizes specific coated titanium anodes (Ru-Ir) due to their efficiency and corrosion resistance in the presence of high chloride concentrations and water.
Advantages Over Other Electrode Materials
Feature | Titanium Electrodes (for Water Electrolysis) | Graphite / Lead Electrodes |
Corrosion Resistance | Excellent in acidic, alkaline, saline | Poor, prone to corrosion and contamination |
Service Life | 5–7 years or more | Typically 6–12 months |
Energy Efficiency | High catalytic activity, low overpotential | Higher overpotential, more energy use |
Environmental Impact | Non-toxic, stable, recyclable | Toxic lead disposal issues, graphite erosion |
Dimensional Stability | Stable size and shape (DSA) | Prone to deformation and short circuits |
Industry Examples and Innovations
Titanium electrodes are at the forefront of advancements in water electrolysis technology:
- Used in small household electrolyzers for generating hydrogen water or disinfecting water.
- Enable efficient and scalable hydrogen production in large-scale industrial hydrogen plants.
- Recent innovations include advanced designs like double-layer titanium electrodes manufactured by 3D printing and sintering, which aim to improve efficiency at high current densities and optimize the use of precious metal coatings.
Technical Specifications (Typical)
Parameter | Value / Range |
Base Material | Commercially pure titanium (Grade 1 or 2) |
Coating | Ruthenium-Iridium oxide, Platinum, Iridium-Tantalum oxide, or custom MMO |
Coating Thickness | 2–40 microns (customizable based on lifespan/performance needs) |
Operating Temperature | Up to 80°C (standard, higher temps possible with specific designs/coatings) |
pH Range | 1–12 (wide applicability) |
Current Density | Up to 8000 A/m² (typical industrial operation around 2000 A/m²) |
Electrode Shapes | Plate, mesh, rod, tube, wire (customizable) |
Service Life | 5–7 years or more (variable by operating conditions and specific coating) |
Partnering with an Expert Supplier
The performance, efficiency, and lifespan of Titanium Electrodes for Water Electrolysis depend critically on the quality of the titanium substrate, the specific composition and thickness of the coating, and the precision of the manufacturing process. It is essential to partner with a manufacturer and supplier specializing in titanium and titanium oxide electrodes with demonstrated expertise in water electrolysis applications.
An expert supplier can provide:
- Technical consultation on selecting the optimal coating type (Ru-Ir, Ir-Ta, Pt, or custom MMO) and thickness for your specific electrolyzer technology (Alkaline, PEM, etc.), electrolyte, and operational parameters.
- High-quality titanium substrates and precise coating application using advanced manufacturing methods.
- Fabrication of electrodes in required shapes and sizes (plates, meshes, tubes, etc.) to fit your electrolyzer design.
- Rigorous quality control to ensure consistent catalytic performance and long-term durability.
- Customized production capabilities to meet unique design requirements or research needs.
Collaborating with such a specialist is vital for obtaining reliable, high-performance titanium electrodes that maximize the efficiency and lifespan of your water electrolysis system.
Titanium Electrodes for Water Electrolysis are indispensable components driving the production of clean hydrogen and enabling effective electrochemical water treatment. Their combination of exceptional corrosion resistance from the titanium substrate and high catalytic activity from noble metal oxide or platinum coatings results in electrodes that offer high energy efficiency (low overpotential), dimensional stability, and a long service life. As the demand for hydrogen and advanced water treatment grows, the role of high-performance titanium electrodes in these vital electrochemical processes will continue to expand.
FAQs About Titanium Electrodes for Water Electrolysis
How to improve the performance of titanium electrodes in water electrolysis?
Performance can be improved by optimizing the coating composition and morphology (e.g., using nanostructures) to increase catalytic activity and surface area, controlling the coating thickness for durability, ensuring strong adhesion between the coating and the titanium substrate, and selecting the correct coating type for the specific electrolyte (acidic vs. alkaline).
What are the main applications of titanium electrodes in seawater treatment?
In seawater treatment, titanium electrodes are primarily used in electrochemical disinfection systems (generating hypochlorite and other oxidants in situ from the salts in seawater) and in ballast water treatment systems for disinfection to prevent the spread of invasive species. They are also used in seawater electrolysis for producing chemicals or preventing biofouling.
What are the advantages of titanium electrodes in ballast water treatment?
Advantages in ballast water treatment include their excellent corrosion resistance in saline seawater, ability to efficiently generate effective disinfectants (like hypochlorite) electrochemically onboard the vessel, long service life in harsh marine environments, and dimensional stability, making them reliable components in compact treatment systems.
What are the main components of the mixed metal oxide coating on titanium electrodes?
The main components of MMO coatings on titanium electrodes typically include oxides of noble metals such as Ruthenium Oxide (RuO2) and Iridium Oxide (IrO2), often mixed with Tantalum Pentoxide (Ta2O5) and Titanium Dioxide (TiO2) which act as stabilizers and promoters.
How to maintain the titanium electrode to ensure its long-term performance?
Proper maintenance involves operating within the specified voltage and current density limits, avoiding contact with harmful substances (like fluorides or certain organics depending on coating), ensuring proper electrolyte flow and temperature, and cleaning the electrode surface gently if necessary to remove scale or deposits without damaging the coating. Regular monitoring of cell voltage can help detect performance degradation early.