In numerous industrial electrochemical processes, selecting an electrode with the right combination of conductivity, corrosion resistance, catalytic activity, and mechanical form factor is paramount. Titanium Tube Electrodes stand out as a highly versatile and robust solution, effectively combining the inherent advantages of titanium with advanced surface coatings tailored for specific electrolytic reactions. These electrodes are tubular structures manufactured from high-quality titanium, coated with active materials like platinum or mixed metal oxides (MMO), making them indispensable in demanding applications from water treatment to heavy industry.
Their tubular shape offers distinct advantages in terms of current distribution and installation flexibility within electrolytic cells, while the titanium substrate provides a lightweight, strong, and exceptionally corrosion-resistant base for the catalytic coating.
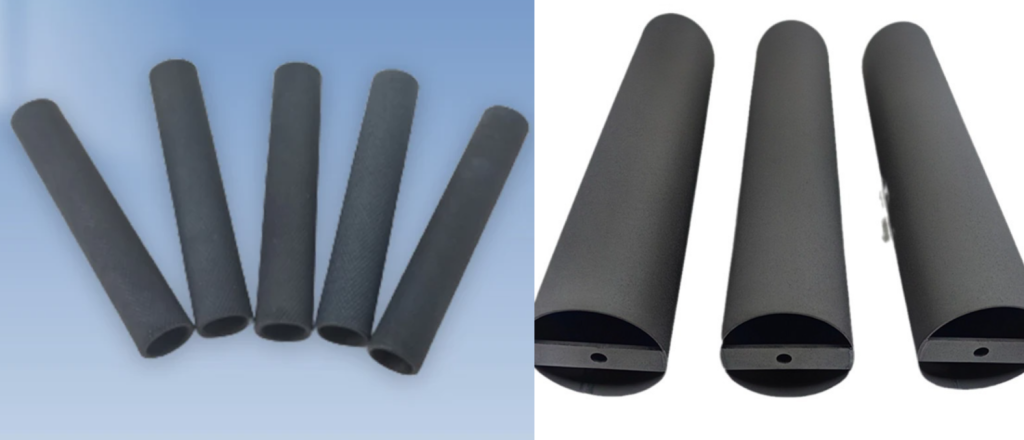
What Makes a Titanium Tube Electrode?
A Titanium Tube Electrode is a sophisticated composite, built upon three key elements:
Titanium Substrate: The core is a seamless or welded tube made from commercially pure titanium, typically Grade 1 or Grade 2. These grades are chosen for their optimal balance of formability, weldability, and exceptional corrosion resistance. Conforming to standards like ASTM B338 ensures the material meets strict chemical composition limits (low levels of impurities like Fe, C, N, H, O) and mechanical property requirements, guaranteeing durability and performance in aggressive electrolytic environments. Titanium’s ability to passivate rapidly means it forms a stable, protective oxide layer, preventing corrosion of the base metal under anodic conditions.
Active Coating: This is the crucial layer that provides the electrocatalytic activity. Titanium Tube Electrodes commonly feature one of two primary coating types:
- Platinized Titanium Tube Electrode: Coated with a thin, uniform layer of pure platinum metal, usually ranging from 0.1 to 20 microns in thickness. Platinized coatings offer electrochemical properties similar to bulk platinum, known for its catalytic activity in various reactions and high conductivity. They are often used where high conductivity and specific catalytic pathways are needed.
- MMO (Mixed Metal Oxide) Coated Titanium Tube Electrode: Coated with a proprietary blend of metal oxides, typically involving precious metal oxides like Ruthenium Dioxide (RuO2) and Iridium Dioxide (IrO2), combined with stabilizing oxides like Tantalum Pentoxide (Ta2O5) and Titanium Dioxide (TiO2). The specific composition is tuned for maximum catalytic activity for reactions like chlorine evolution or oxygen evolution, high electronic conductivity, and exceptional durability and corrosion resistance in diverse electrolytes.
- Platinized Titanium Tube Electrode: Coated with a thin, uniform layer of pure platinum metal, usually ranging from 0.1 to 20 microns in thickness. Platinized coatings offer electrochemical properties similar to bulk platinum, known for its catalytic activity in various reactions and high conductivity. They are often used where high conductivity and specific catalytic pathways are needed.
Tubular Form Factor: The cylindrical shape provides benefits including a high surface area to volume ratio, uniform current distribution from both internal and external surfaces (depending on cell design), and ease of integration into flow-through or concentric cell configurations common in water treatment and chemical processes.
Key Advantages and Benefits
Titanium Tube Electrodes offer compelling advantages over traditional electrode materials:
- Extended Service Life: Especially with MMO coatings, these electrodes demonstrate remarkable longevity, often lasting 15 to 20 years under optimal operating conditions. This is significantly longer than graphite or lead anodes, drastically reducing replacement frequency and maintenance costs.
- Low Operating Voltage: The high electrocatalytic activity of the platinum or MMO coating significantly lowers the overpotential required for the desired reaction, leading to 10-20% energy savings compared to less efficient electrodes.
- Stable Electrochemical Performance: As Dimensionally Stable Anodes (DSAs), they maintain their size and shape throughout their life, ensuring consistent electrode spacing, stable cell voltage, and reliable process control. They do not disintegrate or contaminate the electrolyte or product.
- Superior Corrosion Resistance: The combination of the passive titanium substrate and the durable, corrosion-resistant coatings allows operation in aggressive electrolytes containing chlorine, acids, alkalis, and salts without degrading or contaminating the process stream.
- High Current Density Capability: Designed to perform efficiently and reliably even under high current load conditions required for intensive industrial processes.
- Versatility and Customization: Available in a wide range of standard and custom diameters (e.g., 19mm to 32mm) and lengths (up to 1500mm or more), with various coating options to precisely match the needs of different electrolytic processes and cell designs.
Diverse Applications in Industry
The combination of durability, efficiency, and form factor makes Titanium Tube Electrodes suitable for numerous critical applications:
- Water and Wastewater Treatment: Widely used for electrochemical disinfection (generating chlorine or hypochlorite), oxidation of persistent organic pollutants, and general electrochemical treatment processes. The tubular shape is excellent for reactors with fluid flow.
- Electroplating and Metal Finishing: Serve as robust anodes for hard chrome plating, as well as plating of copper, zinc, nickel, and other metals. Platinized tubes are often preferred in specific plating baths.
- Chlor-Alkali Industry: MMO-coated titanium tubes are utilized in certain cell designs for the production of chlorine and caustic soda, providing stable, long-lasting performance.
- Cathodic Protection: Especially MMO-coated tubes, are standard impressed current anodes used to protect structures like pipelines, storage tanks, jetties, and marine vessels from corrosion, including in demanding seawater environments. Their long life and reliable performance are crucial here.
- Chemical and Electrochemical Synthesis: Provide stable and efficient anodic reactions for the production of various organic and inorganic chemicals.
- Other Industries: Found in applications within aerospace, marine engineering, power generation (e.g., cooling water chlorination), and instrumentation where durable, corrosion-resistant electrodes are required.
Physical and Mechanical Properties
Built from commercially pure titanium, these electrodes possess:
- High mechanical strength and fatigue resistance.
- Low density (lightweight).
- Excellent resistance to various forms of corrosion, including pitting, crevice corrosion (with proper design and handling), and erosion corrosion.
- Available in standard and customized dimensions to fit specific cell configurations.
Choosing the Right Titanium Tube Electrode
Selecting the optimal Titanium Tube Electrode involves evaluating several factors:
- Electrolytic Process & Chemistry: The specific reaction (Cl₂ evolution, O₂ evolution, etc.) and the composition of the electrolyte (pH, temperature, presence of chlorides, sulfates, organics) are the primary drivers for choosing the appropriate coating type (Platinized vs. MMO) and its specific formulation.
- Current Density Requirements: Determines the necessary coating thickness and design to ensure long life and performance.
- Cell Design: The tubular shape must integrate effectively into the electrolytic cell.
- Required Lifespan: MMO coatings generally offer longer life, particularly in corrosive OER environments.
- Budget and Total Cost of Ownership: While the initial cost includes precious metals, the energy savings and long lifespan often result in significant long-term cost benefits.
Partnering with an experienced manufacturer capable of understanding your process needs and offering customized solutions is key to obtaining the most efficient and cost-effective electrode.
Partnering with an Expert Supplier
The quality and performance of Titanium Tube Electrodes rely heavily on the manufacturer’s expertise in titanium fabrication, surface treatment, and advanced precious metal/MMO coating technologies. A leading supplier specializing in titanium and titanium oxide electrodes brings the necessary technical knowledge, rigorous quality control, and manufacturing capabilities to produce high-performance Titanium Tube Electrodes that meet stringent industry standards. Look for partners who can provide technical support and offer customized production in terms of substrate size, titanium grade, coating type, composition, and thickness to perfectly match your specific application requirements, ensuring reliability and optimal operational efficiency.
FAQs About Titanium Tube Electrodes
What is the lifespan of titanium tube electrodes?
The lifespan varies depending on the coating type and operating conditions. Platinized electrodes typically last several years. MMO-coated titanium tube electrodes are known for their exceptionally long life, often reaching 15 to 20 years under suitable operating conditions, significantly exceeding the life of traditional electrodes.
How is the performance of titanium tube electrodes in different electrolytes?
Their performance is excellent across a wide range of electrolytes, including acidic, alkaline, and saline solutions. The specific coating is chosen based on the electrolyte and the desired electrochemical reaction. MMO coatings are highly resistant to corrosive environments and are tailored for specific reactions like oxygen or chlorine evolution.
What are the main materials of titanium tube electrodes?
The main materials are a titanium substrate (typically commercially pure Grade 1 or Grade 2 titanium) and an active coating. The coating is either platinum or a Mixed Metal Oxide (MMO) composed of oxides of precious metals like ruthenium and iridium, often mixed with stabilizing oxides like tantalum and titanium oxide.
What are the applications of titanium tube electrodes in seawater?
Titanium tube electrodes are widely used in seawater applications, primarily for cathodic protection of marine structures (jetties, platforms, ships) and pipelines, and for seawater electrolysis to produce hypochlorite for disinfection or other chemical processes. MMO coatings are particularly suited for the high chloride content and corrosive nature of seawater.
Titanium Tube Electrodes, whether platinized or MMO coated, are critical components enabling efficient and sustainable electrochemical processes across a multitude of industries. By leveraging the superior corrosion resistance and mechanical properties of titanium in a versatile tubular form factor, combined with highly catalytic and durable coatings, these electrodes offer unmatched longevity, energy savings, and stable performance in demanding environments. Their ability to be customized further enhances their value, making them an indispensable choice for modern electrolysis, plating, water treatment, and cathodic protection applications.